In September 2021, LIFTbuild began construction on the Exchange building in Detroit’s Greektown neighborhood using a Vertical Manufacturing℠ approach. The roof of the 207-foot-tall condo and apartment tower was constructed and placed first, followed by the top floor and then each successive floor before reaching the conventionally-built first and second floors. By the end of construction, floors were raised in just nine-day cycles, which is the amount of time it took to fully prepare each level.
As every 500-ton, 11,000-square-foot floor was completed, it was raised using strand jacks, pulley systems and a proprietary steel-frame rigging system. Successful delivery of Exchange is proof of concept for LIFTbuild.
As the first-of-its-kind project in the world, LIFTbuild was challenged to think innovatively and use cutting-edge tools for successful project completion.
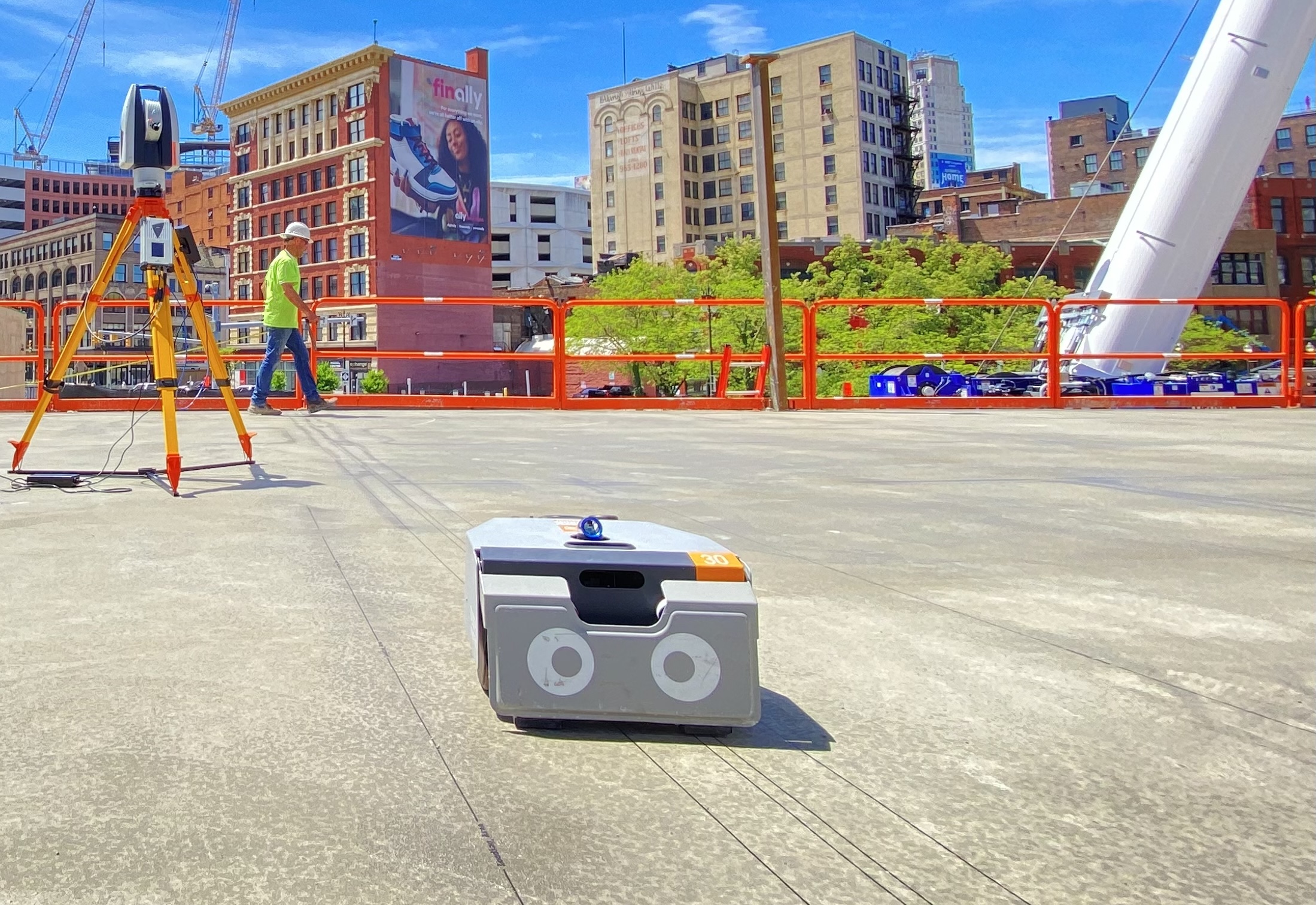
Complex Project Leaves No Room for Error
Pivotal to construction success were layouts by Dusty Robotics. The technology solved a challenge LIFTbuild otherwise would not have resolved so confidently or efficiently. Materials needed to complete each level’s interior were loaded onto the floor before being hoisted into place. Materials needed to be loaded strategically and according to the structural engineer’s requirements to maintain balance during lifting.
Dusty Robotics marked the correct layout for material placement and weight distribution to maintain the balance needed to lift each floor into place safely. Without Dusty Robotics, there would have been no precise way to ensure all materials were loaded correctly to maintain the necessary balance.
Dusty Robotics Increases Project Efficiency
By the end of the project, each floor was laid out by one employee in one eight-hour shift using Dusty Robotics. Comparatively, traditional layout methods take approximately four days per floor. Layout staff spent more time doing manual calculations to fact check the layout against the model–ensuring accuracy.
In addition to meeting balance requirements, Dusty Robotics laid out the placement of materials in specific zones on each floor to allow subcontractors to complete interior work efficiently. Materials were placed in the areas where they would be used and away from future wall locations, avoiding the need to move materials around once the floor was in place.
Multi-trade layout Eliminates Rework
Dusty Robotics’ multi-trade layout printing capability allowed subcontractors to work more efficiently on the Exchange project, as their layouts were completed by Dusty Robotics before they arrived onsite. Each trade only needed to fact check the layout before beginning work.
The layout on Exchange was 100% accurate to the model, which decreased the margin of error accepted by traditional layout methods. For example, ¼ inch is the standard margin of error for framing and mechanical contractors, and ½ inch is standard for plumbers. If a framer’s manual layout is off by ¼ inch, it can have severe implications for subsequent contractors–steamrolling into a larger, more time-consuming and expensive problem. As rework typically accounts for 10% of the total project cost, 100% accuracy significantly impacts the budget.
Exchange was completed in July 2023 on budget and according to schedule for approximately $70 million.
LIFTbuild has revolutionized the project life cycle with a fully integrated approach to building high-rises, from concept to completion. The technology leverages a generative design process to identify optimized building configurations. Project delivery takes a Vertical Manufacturing approach, creating a construction site that is safer, more efficient, and cost-effective. LIFTbuild is a member of the Barton Malow Family of Companies.
Interested in learning more about the
Dusty FieldPrinter?
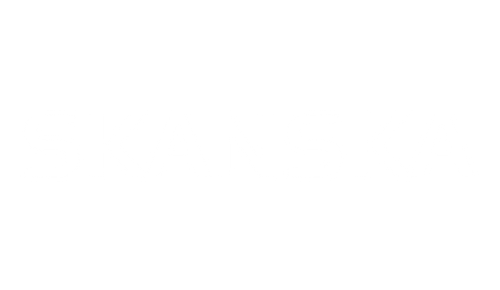
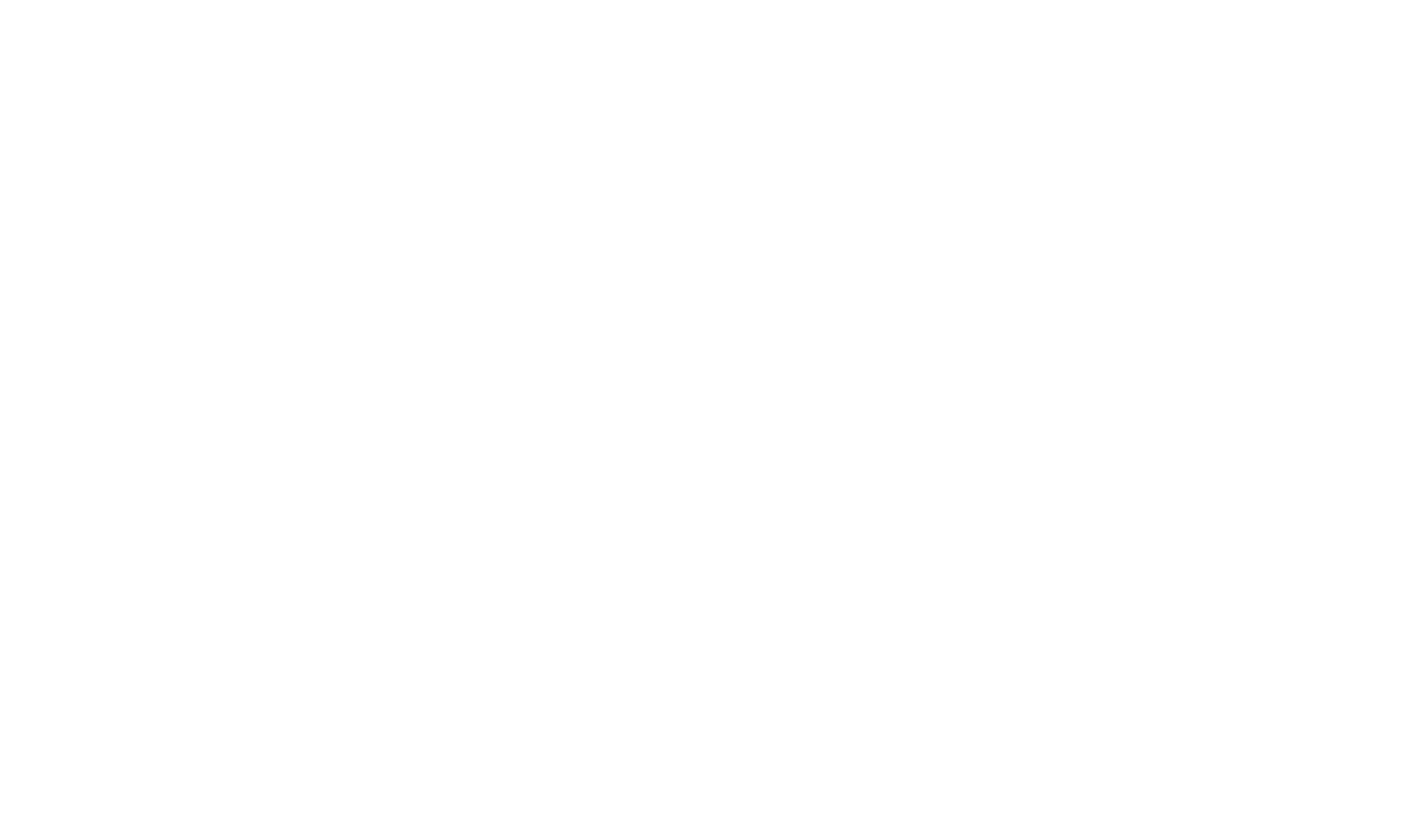
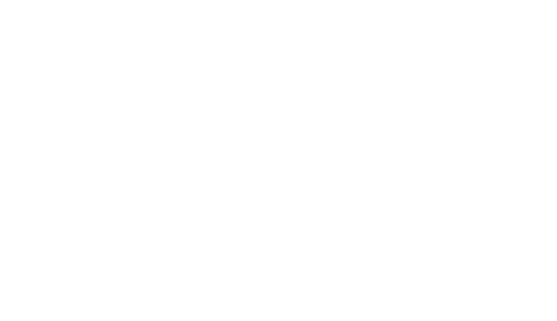
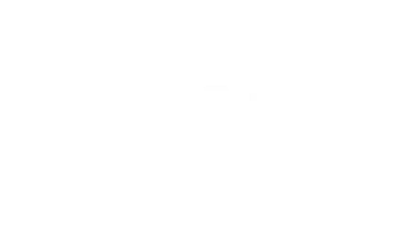
.png)
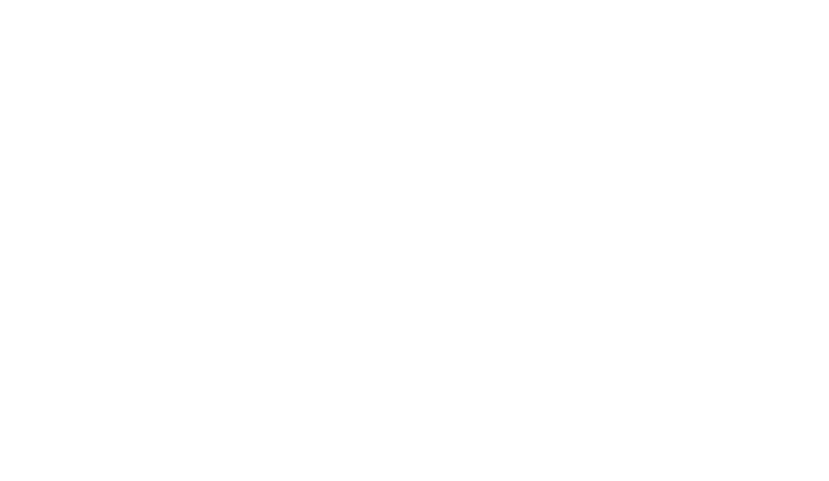