The Cost of Rework in Construction & Strategies to Avoid It
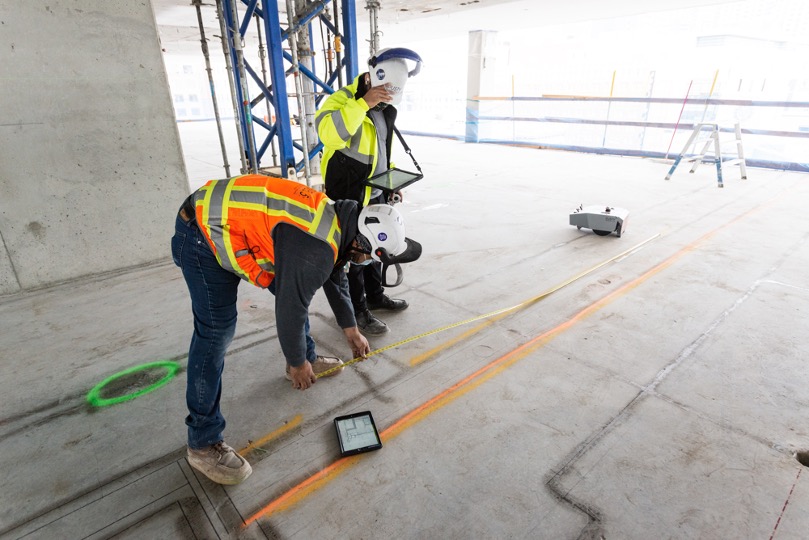
Rework is a relentless phantom that haunts every construction project. It is expensive, time-consuming, and hinders project completion. However, there are ways to “work smarter” and prevent a substantial amount of rework from needing to take place.
Here, we will explain the high, hidden costs of rework and introduce strategies that will help you maintain your balanced budget and schedule, no matter the size of your construction project. By addressing the pain points that lead to rework, we will empower you and other industry professionals with the knowledge and tools necessary to keep rework to an absolute minimum.
What is Construction Rework?
Nothing bloats a construction project’s budget and timeline like rework. Rework occurs when there are errors in the design process, inaccuracies during layout, modifications to the existing work, repairs to existing work, or design changes that require redoing completed work.
A little bit of rework is likely on any project, even if it’s just because a client changes their mind about something. But rework has many substantial impacts on your project, especially if the work is more than just minor design changes.
The Financial Impact of Rework
In general, rework and conflict resolution costs the construction industry more than $177 billion annually in the US. This massive cost is a huge monetary burden and carries other major indications of financial impact.
- Direct costs: Studies have found that rework can be anywhere from 9% to 20% of a project’s total cost.
- Extended project timelines: About 30% of the work done at construction sites is actually rework, requiring a substantial amount of time.
- Increased material waste: Rework requires you to spend more on redundant materials.
- Impact on project profitability: Construction rework creates up to 300% of a project’s productivity losses. The lower your productivity, the less profitable your project will be.
- Reputational damage: If your firm is spending too much of the client’s time and money on rework, customer satisfaction drops. Rework can cause a delay of nearly 10% of the project’s timeline, which irritates customers and damages your reputation.
- Safety risks: Because rework eats into your timeline and restarts dangerous installation tasks, safety risks and construction injuries go up as your crew hurries to complete the rework on time.
Top 5 Causes of Rework in Construction
There are several stages in the construction process where the need for rework can develop. Here are the major pain points that lead to rework.
1. Design Errors or Discrepancies
Inconsistent or conflicting information between mechanical layout, drywall layout, and electrical and plumbing layout can lead to serious discrepancies that require rework. Mistakes may also be made during the manual layout process, as your crew manually translates the digital model to the construction site surface.
2. Communication Breakdowns
Rework caused by poor communication on projects is responsible for about half of all construction rework time and accounts for over $31 billion dollars of rework costs. With manual layout, individual trades stagger the measuring and marking of each layout, opening the project to miscommunication and mistakes. Misalignment between trades’ layout results in further finger pointing and communication breakdowns in order to identify and settle the rework costs.
3. Inadequate Planning and Changes in Project Scope
Sometimes the cause of rework has nothing to do with a construction site’s conditions and everything to do with what happens before the ground is even broken. Nearly 80% of cost deviation on projects comes from changes to the design; only about 17% are related to construction activities.
4. Lack of Skilled Labor or Training
Rework also results from the construction labor shortage. A combination of an aging workforce, job loss during the Covid-19 pandemic, and other factors have led to a decline in the amount of skilled labor available for construction jobs. Without capable, skilled labor and adequate training programs, mistakes and injuries are more likely to impede construction success.
5. Material or Equipment Issues
Finally, improper equipment and poor quality material may also cause rework. Regardless of accurate designs and flawless layout, high-quality installation still requires high-quality materials and equipment.
How to Reduce Construction Rework
There are several intervention strategies that can help you prevent rework on your construction projects. These strategies will help to compress your schedules, increase efficiency, and improve profitability.
Utilize Construction Technology
To prevent errors in the layout process and ensure accurate installation the first time around, use robotic layout. This technique utilizes a robot that can print your coordinated digital model directly on the construction site surface, like the Dusty Robotics FieldPrinter®. With all trades’ layout printed in a single pass with 1/16” accuracy, you can guarantee that what you design is what you build, reducing rework and improving trust, clarity, and efficiency.
Discover how Skanska, one of the world’s largest construction and development companies, used automated layout to reduce rework by 75%.
Robust Project Planning
Preventing rework starts at the very beginning of the construction project– the project planning. So much rework can be prevented if all project stakeholders maintain clear communication with each other during planning. Digital design models improve communication substantially, enabling all trades to work directly in a centralized model.
With a single source of truth, all stakeholders can stay on the same page as much as possible during the planning process. Moreover, robotic layout brings your coordinated digital model directly into the field with fully automated layout, ensuring you maximize the benefits of your robust project planning while reducing rework.
Emphasize Quality Control
Frequent quality inspections and routine observations should be conducted regularly on any project. This will allow you to spot rework items early, or even before they happen. Make sure to bake quality checks into your project workflows, notably during layout and installation.
Improved Collaboration and Teamwork
With several stakeholders involved in construction projects, collaboration determines success. When trades work in isolation, communication errors and misalignment are more likely to cause delays, rework, and costly issues. Embracing cross-trade collaboration during design, layout, and installation will help ensure your project runs smoothly. This improves the collaboration between plumbing, electrical, HVAC, and more.
Dusty Robotics FieldPrinter facilitates collaboration by printing the coordinated digital model for all trades in a single pass. Members from each trade can walk the floor together, confirming alignment before installation. This removes the risk of miscommunication or errors in trade layout, obviating the need for finger pointing and costly rework down the line.
According to Noah Bull, a project engineer at Level 5 Inc., his team has “been able to find a lot of issues with MEPs and plumbing that might be off and fix that before we start any framing. That right there is saving us a huge amount of money.”
Training and Skill Development
Finally, you can address the skilled labor gap by offering training and skills development. While this may have a higher up-front cost, you can think of it as an investment into your project– and your crew.
How Dusty Robotics Can Help You Avoid Rework Costs
There’s an old saying: An ounce of prevention is worth a pound of cure. One of the most effective ways to reduce rework and ensure that the work is done correctly the first time is to ensure accurate and aligned layout. When you use the Dusty FieldPrinter, you can compress your construction schedules, prevent rework, and ensure a successful construction process.
Contact us today to find out how Dusty Robotics can improve your construction projects!