Dusty Streamlines Mortenson’s Data Center Mega Project
Mortenson, an ENR top 30 general contractor and developer, is an expert in mission critical data center and complex construction projects. The team is working on a $1B project encompassing two data centers, totaling 700,000 square-feet, for one of the largest data center owners in the country and chose Dusty Robotics as their multi-trade automated layout solution to streamline the massive project.
“Dusty is perfect for huge and complex buildings like data centers,” says Travis Brock, Senior Integrated Construction Coordinator. “Dusty unifies the model and the install to eliminate conflicts in the field and makes the layout process very quick and fluid.”
Dusty Helps Elevate Hyper-Scale Data Center Builds
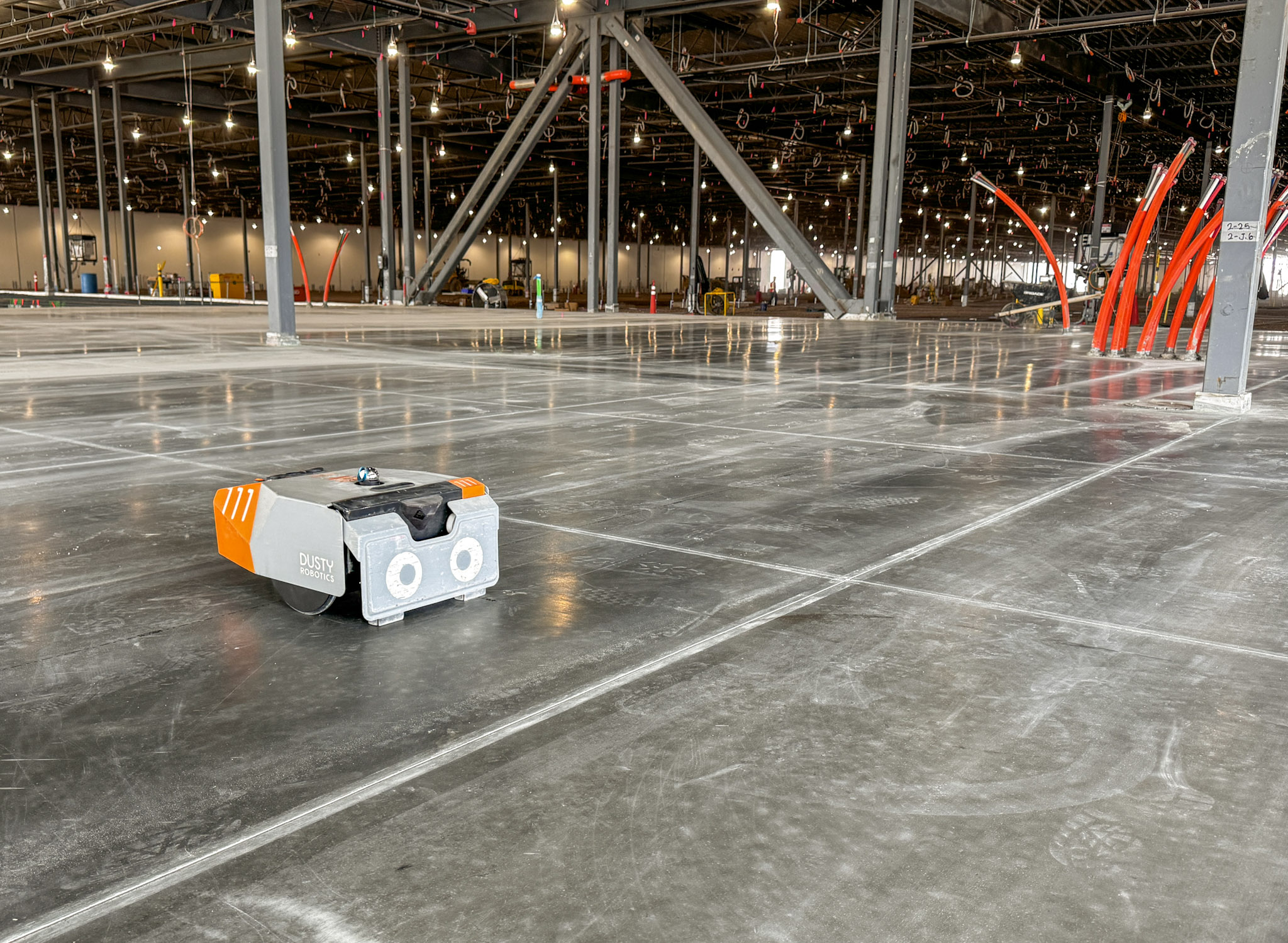
Typically, a similar project would require all trades to do their own layout based on designated control points. Fast-moving projects with multiple design changes can cause outdated plan sets, and this incorrect information can result in a misaligned or incorrect layout. Dusty translates the 3D model into a 2D drawing in the field, so there’s no communicating the model from person to person and issues caused by outdated plans are eliminated.
“Using traditional methods, you always end up with something laid out where it’s not supposed to be, which can cause rework for contractors and leads to schedule delays to identify the cause of the problem,” Brock says. “Dusty takes all those potential inaccuracies and eliminates them because everyone on the project uses the same model, and they can trust that model is accurate. With Dusty, errors or conflicts are identified and fixed early, before they become a problem.”
Dusty allows everyone to trust that the printed layout is the same as what’s on the 3D coordinated model. They can verify the printed layout with the model while in the field, and they trust that it is a single source of truth.
“We’ve come a long way in the last couple of years with 3D modeling and Dusty has continued to push the way we’re used to doing things,” says Mortenson’s Senior Integrated Construction Manager Abbey Mumford. “3D models have been available to field team members on mobile devices for a few years, but now with Dusty, this information is directly transferable and visible in the field.”
Dusty Streamlines Layout for Multiple Trades
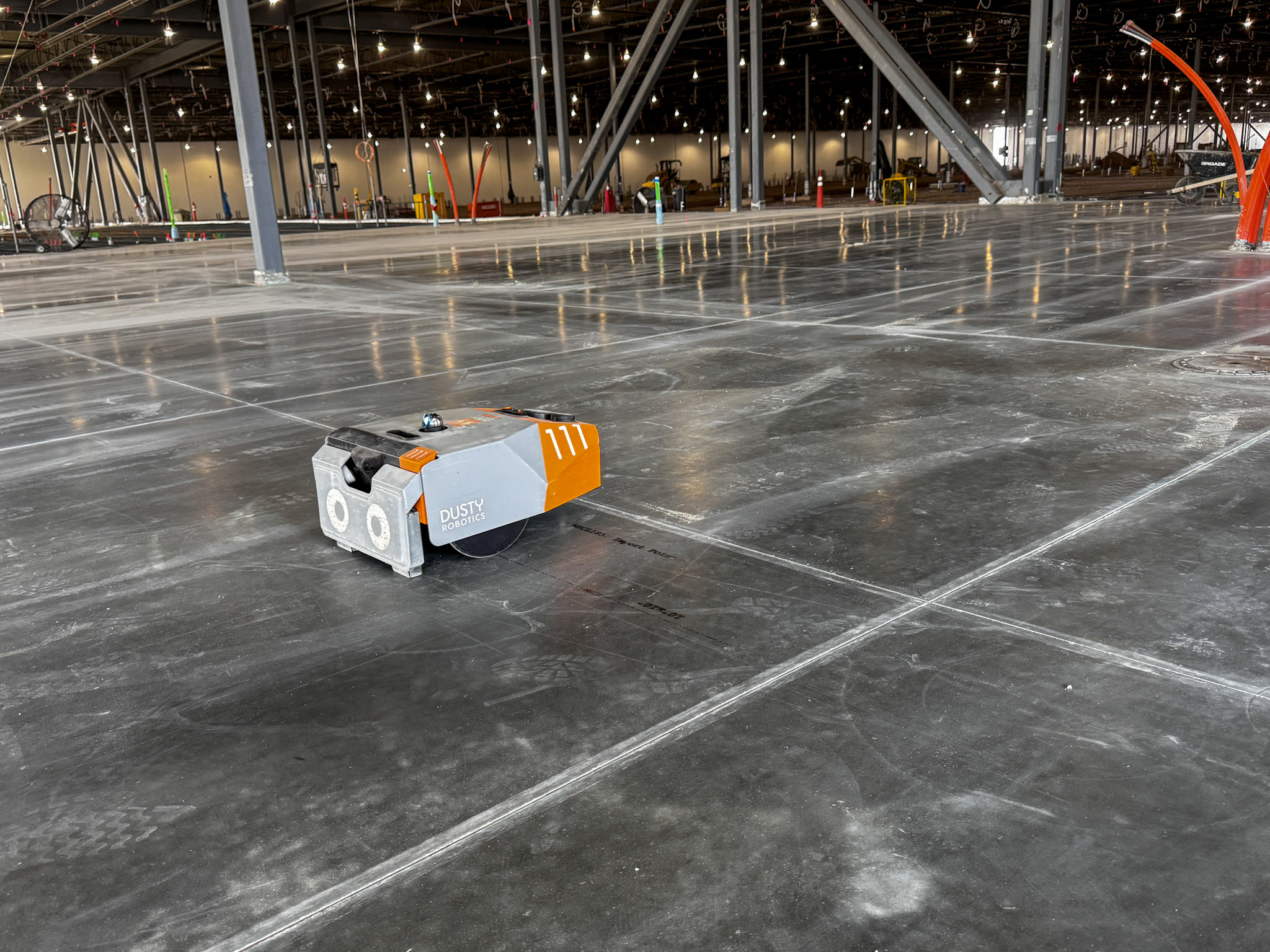
The FieldPrinter system was initially scoped to lay out walls and for the mechanical contractor, Southland Industries, to print mechanical duct and piping, as well as hanger and anchor locations inside the building. Other trades on the project saw the advantages Mortenson and Southland were gaining by using Dusty and opted in to use this technology for their own layouts.
“After being consistently accurate and seeing us have the ability to put walls up almost immediately behind Dusty, other trades got on board,” Brock says. “We moved through the building much more quickly because we were not spending the time for every trade to go in and lay out.”
Training from Dusty’s customer success team helped drive buy-in too. The Mortenson team initially had a Dusty representative on site to train the team and ensure their continued success on the project. Dusty representatives also set up meetings with trade partners as they decided to use Dusty for layout.
Brock explained, “The Dusty customer success and implementation teams felt like a part of our team and made it so we never had to wait for answers.”
Getting each of these trades to collaborate directly helped save time on the very tight project schedule. Mumford saw the benefits of multi-trade layout. She said:
Dusty Adds Efficiencies to Manufactured Components
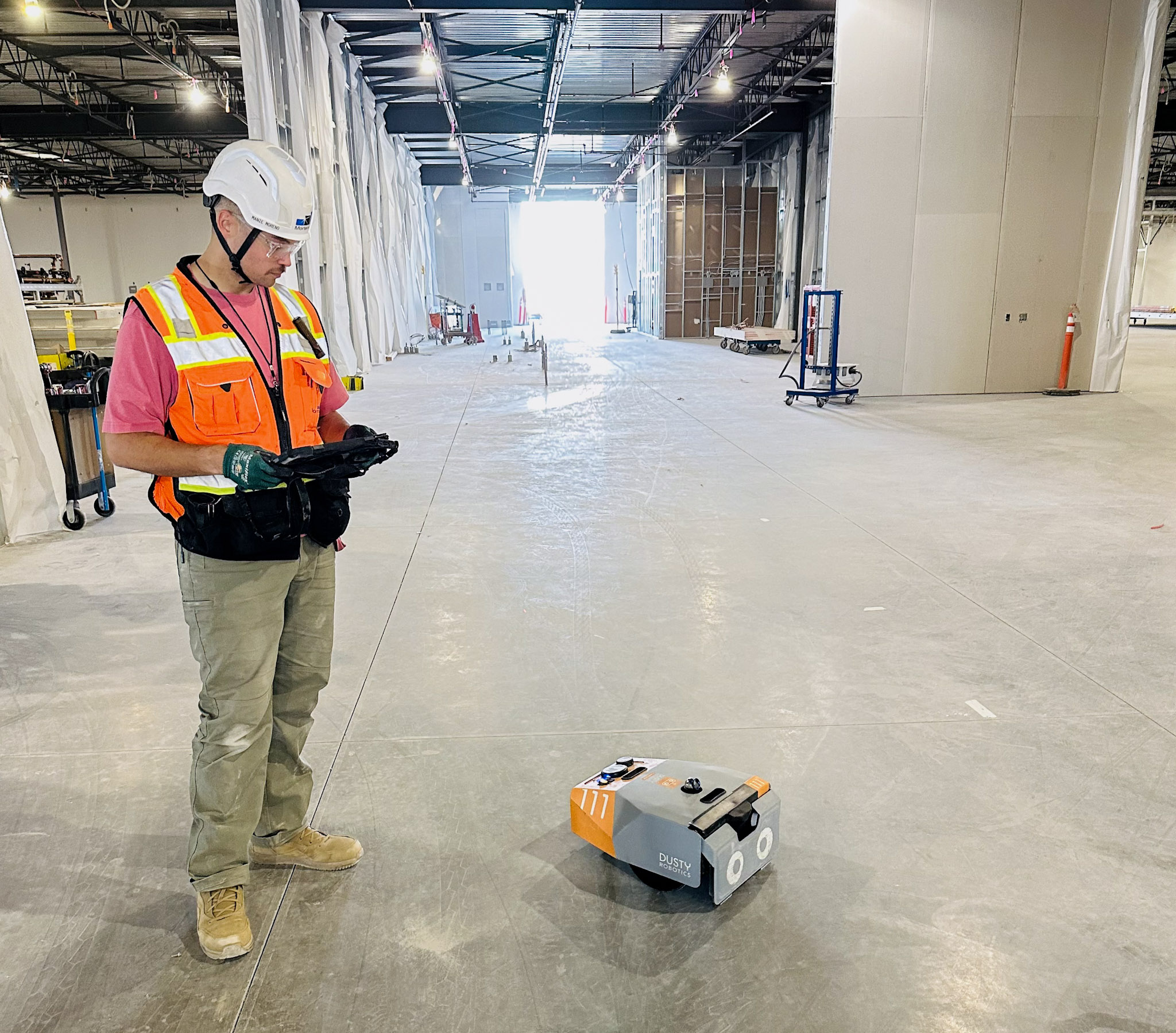
The data center includes many elements manufactured off site that were laid out with Dusty. Because prefab elements were coordinated early, the team was confident in their placement and avoided unnecessary work. When it was time for install, the prefab elements were installed quickly and accurately according to the printed layout.
“We have a series of racks that carry a lot of the mechanical piping and some of the other utilities that were all built off site and modeled,” Brock says. “Previously, we would build a piece in place, or we would bring it in, align it to mark the floor and then move it back out, drill the anchors and then reset it. Dusty eliminated several steps in the process to get the racks installed.”
The building included prefabricated wall panels as well. Typically, layout would only include entire walls. Dusty allowed Mortenson to lay out and name each individual panel.
“With Dusty, the team knew exactly where prefabricated components went without having to pull out drawings, as well as the panel break locations,” Brock says. “If there was a problem with a panel, they could identify the panel number and quickly find it on the floor.”
Mortenson used Dusty’s ability to lay out text as well as lines to label points for various project systems, which helped eliminate confusion and reduce re-work during install. For example, the team labeled key information at the top and bottom of cable tray openings, which ran through the framed walls, on the floor so the framers did not have to look at prints. Instead, the framers could trust the Dusty layout and focus on their scope of work.
Dusty proved to be an invaluable tool on this massive data center project, saving the team time, money, and manpower during layout and throughout the course of construction.
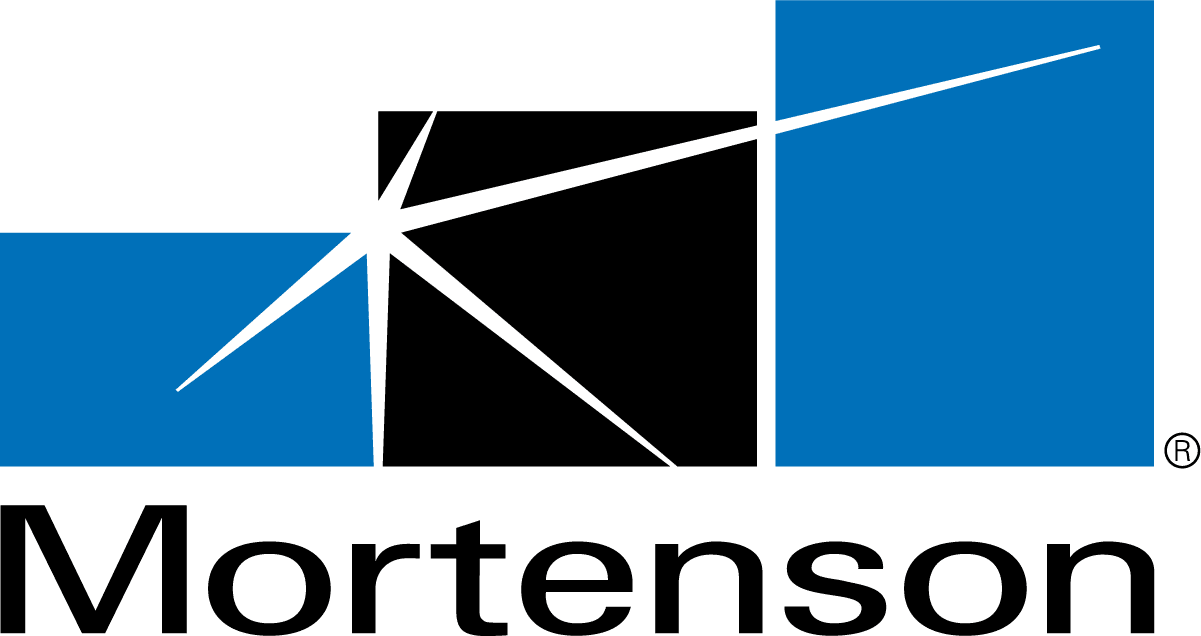
Mortenson is working on a $1B project encompassing two data centers, totaling 700,000 square-feet, for one of the largest data center owners in the country and chose Dusty Robotics as their multi-trade automated layout solution to streamline the massive project.
Interested in learning more about the
Dusty FieldPrinter?
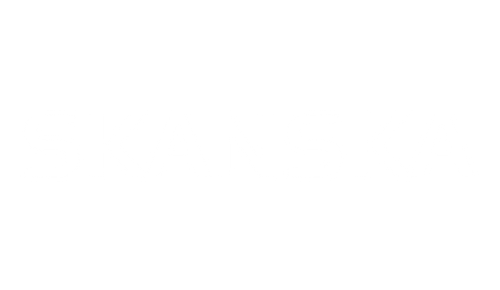
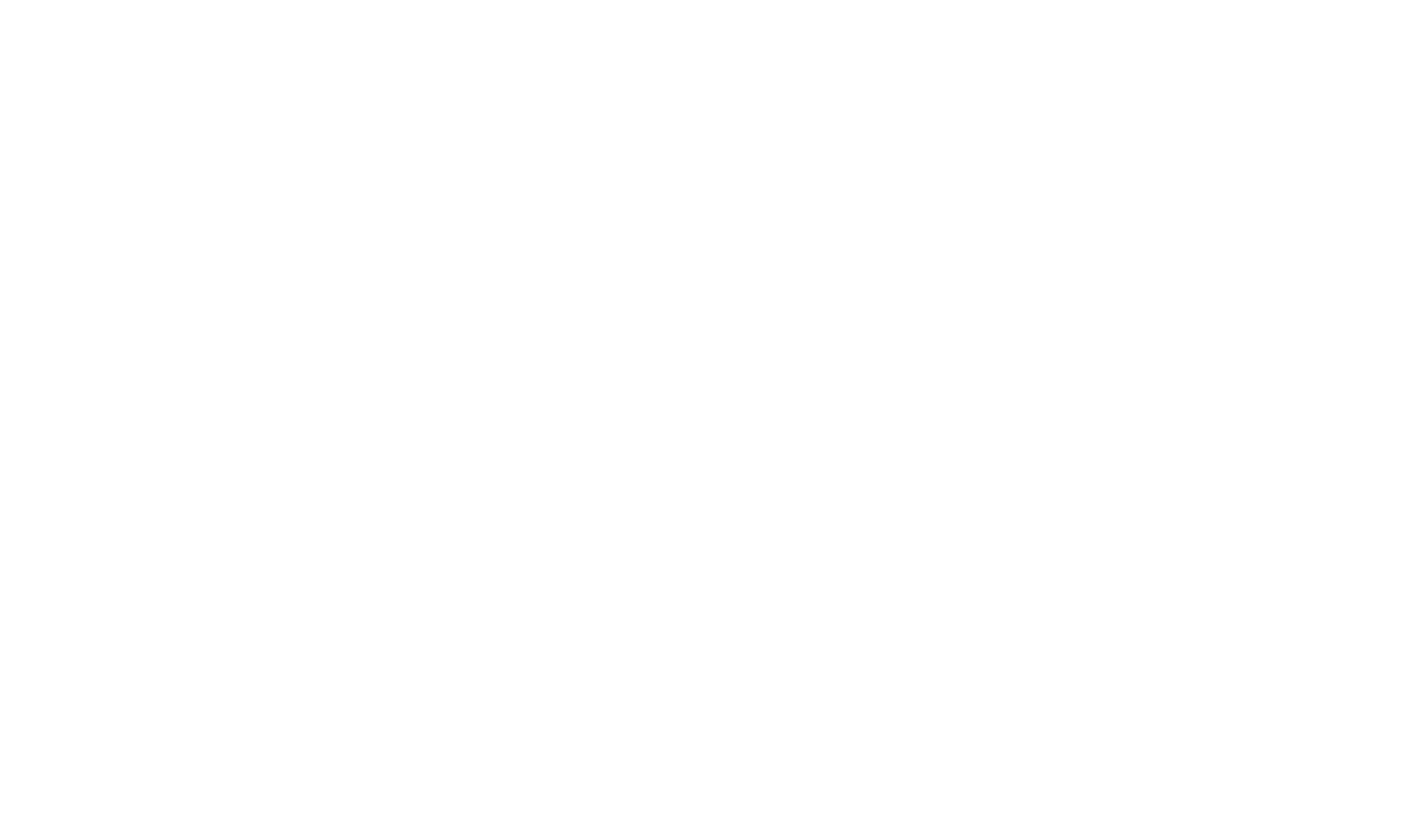
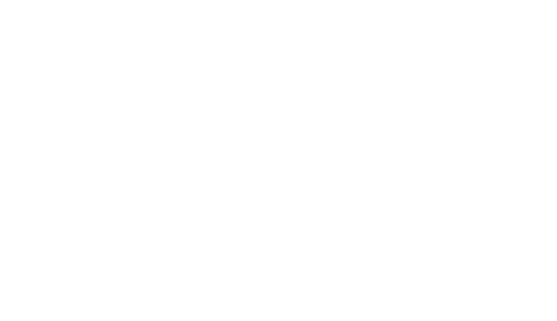
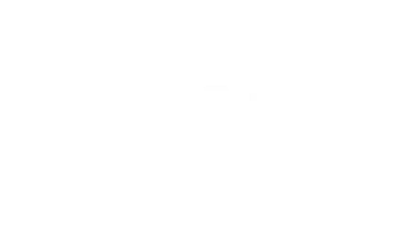
.png)
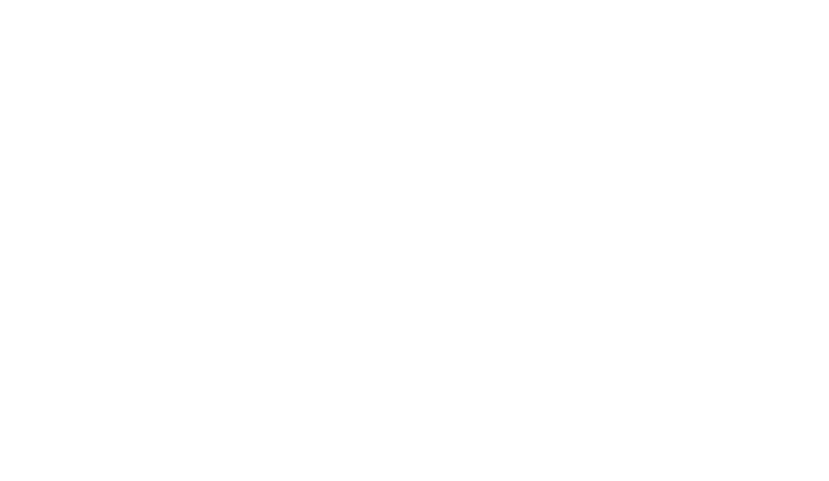