A Framer’s Guide: Executing with GCs on Automated Layout
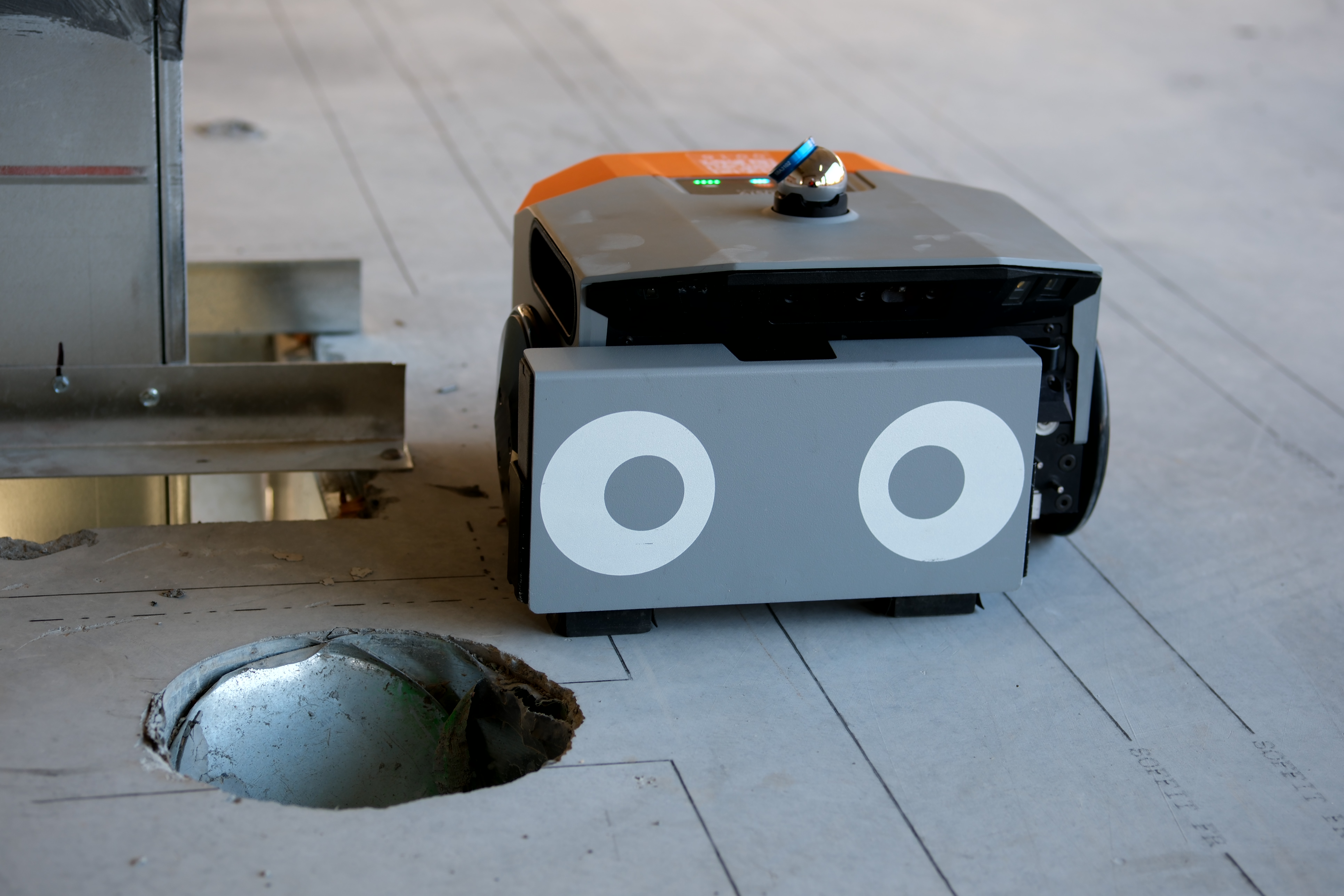
➜ This article is for you if you’re a framer creating an effective automated layout workflow with a supportive GC.
As a framer adopting automated layout, you’re not just improving your operations—you’re also influencing other stakeholders, like the GC, to embrace this innovation. Once the GC is on board, the next step is to strategically leverage their support to maximize automated layout’s effectiveness for everyone involved: you, the GC, and the project as a whole.
Here are some key adjustments you can request to optimize the process:
Files: Access to a coordinated BIM model
Dusty shines as a communication bridge between VDC and execution on the jobsite. To prep for automated layout, you’ll want access to the coordinated BIM model. Depending on the degree of your firm’s involvement in VDC for the project, you may already have that access, or you might need the GC’s help to get it.
If the project doesn’t use a full VDC process, automated layout is still possible by working with the architectural design model. The further removed the files you receive are from the source-of-truth model, the more in-house work you’ll have to do to be ready for automated layout. So if you request the Revit file but receive 2D CAD files instead, it’s worth trying again. As the innovator on the project team, you understand what digital assets are critical to success—often better than others on the team. Patience, and the GC’s support, will help you communicate your needs effectively.
Jeremy Evans, Design Manager at KHS&S Construction, shared his experience: “I would suggest Dusty Robotics to anyone who needs quick, fast, and easy layout. You just need to put in the work upfront on the model, and the layout is easy.”
Process Improvement: Clear jobsite floors
You may need to ask the GC to adjust sequencing on the jobsite, framing these requests as improvements benefiting the whole project. A clear, open floor enables you to complete layout far faster. While Dusty can print in various conditions, a clutter-free surface allows for significantly quicker layout, compared to piecemeal access where materials are shifted as layout progresses.
Automated layout’s speed benefits everyone—framer, GC, and project—making the adjustment worthwhile.
Schedule Accommodation: Sequencing Correctly
Consider asking the GC for small schedule tweaks. For instance, if the GC likes to avoid empty-house days by having plumbers install risers while reshoring is still in place, these risers can later become obstacles for robotic layout. Although Dusty’s FieldPrinter 2 can navigate around such obstacles, the process slows down. Having risers installed after layout is complete is faster overall, benefiting the project and owner, though it may require the GC to alter their usual workflow.
Coordination Improvements: Alignment with Other Trades
Automated layout enables a transformative shift: multi-trade layout. This approach involves framing, MEPs, and other key trades using the same coordinated model to lay out their work at the same time. The result? The jobsite floor becomes a full-scale print of the model, serving as a shared reference that shows how each trade’s work coordinates with others’. This clarity reduces conflicts and boosts efficiency across the board.
Helen Schneider, Senior Associate at Perkins & Will, highlighted this advantage: “We can come out in the field and see that information on the slab in real-time, we can review it with the electricians, we can review it with the framers and we can detect clashes together in person.”
Collaborating with the GC on automated layout strengthens your working relationship, ensures you maximize the benefits of the process, and positions your business as a high-value partner.