A Framer's Guide: Getting GCs Onboard with Automated Layout
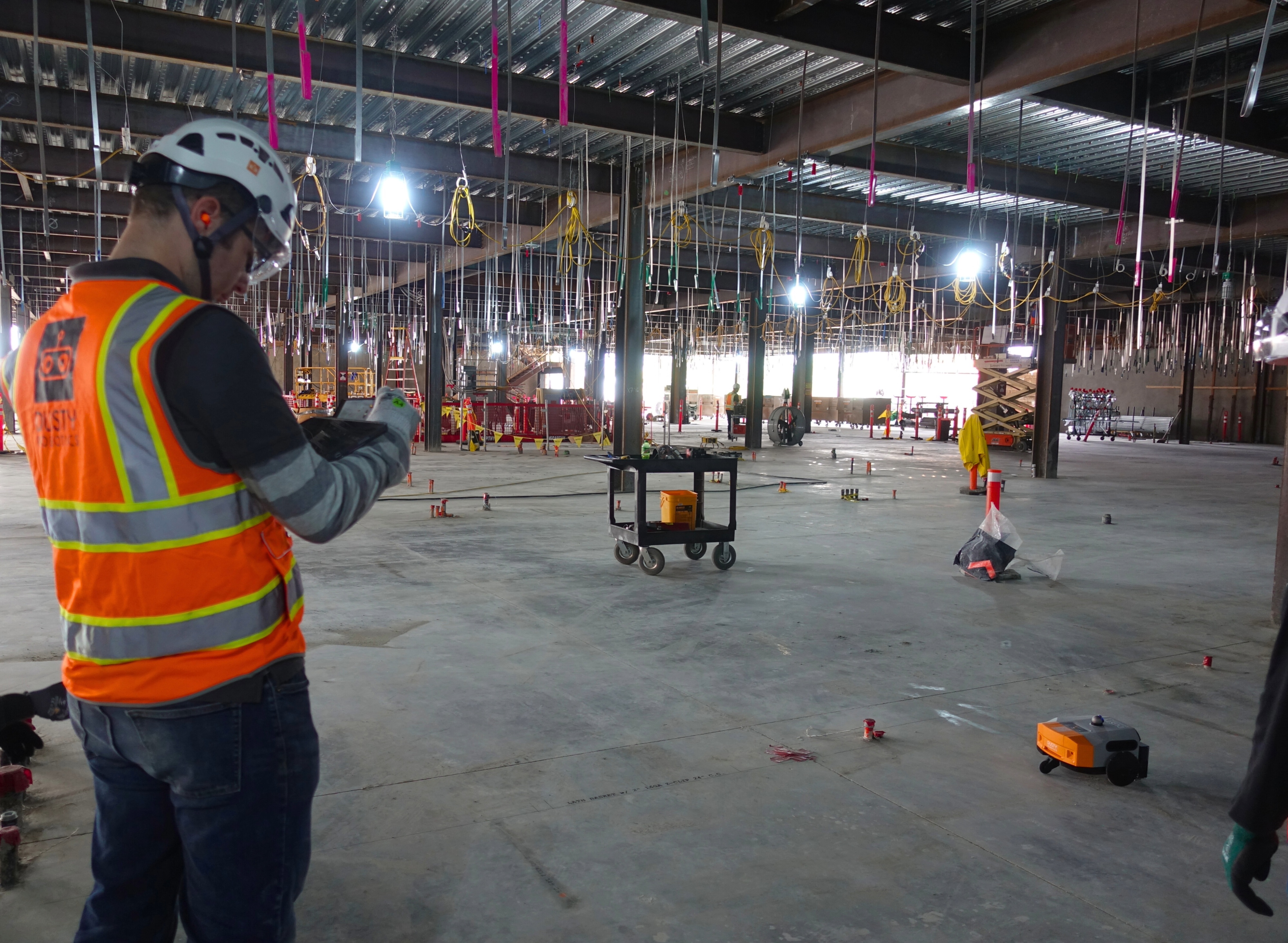
➜ This article is for you if you’re a framer who needs to get your GC onboard with automated layout.
If you’re a framing contractor using automated robotic layout, you’re on the road to transforming your projects by connecting field teams to the full depth of information in your digital models. Gaining GC support will amplify these benefits, positioning your business as a preferred partner. The good news? Most GCs will be enthusiastic once they understand the value of your process—you just need to communicate it clearly.
Aligning the GC to Automated Framing Layout
When the GC is aligned and engaged in your automated layout process, they gain visibility into the steps you’re taking to ensure positive project outcomes. This isn’t just about faster layout. You’re pulling information out of the model and onto the jobsite where it can benefit everybody. You’re improving the quality of your work, and reducing the risk of re-work for everyone else on the project. Put simply, you’re making the GC look good to the project owner, and positioning your business as a preferred partner.
Jeremy Evans, Design Manager at KHS&S Construction, reflected on a Dusty-powered project: “Dusty changed a lot of minds, proving that something so complex could go so smoothly. The owners, general contractor, and other trades watching it take form were in awe.”
Automated Layout Reduces Project Risk
If you really want to get a GC excited about a new idea, focus on risk reduction. GCs view projects through a risk management lens, and automated layout directly addresses that concern.
With automated layout, you’re eliminating communication gaps that cause defects. This prevents rework, delays, and cost overruns—while also avoiding difficult conversations that could hurt the GC’s standing with the owner.
Automated layout isn’t just faster; it makes your crew more productive by providing precise, detailed information from the model. Printing all layout at once also reveals conflicts early, giving everyone more time to identify and resolve problems. In contrast, less sophisticated framers might only snap priority walls initially, leaving interior walls for later—missing opportunities to uncover issues early.
The layout you print also becomes a communication tool. You give the GC an asset that supports early job walks and helps other trades avoid mistakes. For example, it’s far easier for an electrician to recognize they’re about to order the wrong mud rings when they see you’ve laid out two layers of gyp for a fire-rated wall assembly. Even though these insights extend beyond your scope of work, they make a big difference to the GC.
Printing Extra Information for Project-Wide Impact
Offering to print additional layout details can enhance the efficiency of other trades and increase your value to the GC. Here are a few ways to do that:
- Control and grid lines: Dusty’s robot needs only three control points to align the digital model in physical space. It can print grid lines, even embedding their labels into the line style, eliminating the need for surveyors to snap lines manually. This speeds up layout for all trades, even those using traditional methods.
- Contextual information: Print elements like ADA clearance radii to aid job walks and ensure compliance. Identifying clearance issues early can prevent costly corrections and leave a positive impression on inspectors.
- Object tags, Printing room names, door identifiers, and other labels makes it easier for all trades to find the information they need to stay productive.
- QR codes linked to project documentation: These can connect to the GC’s construction management system (e.g., Procore or Autodesk Construction Cloud) or cloud storage platforms (e.g., OneDrive, Dropbox). This makes it easy for the team to access information and updates directly from the layout on the floor.
Position Your Business As a Leader
Securing GC alignment with your automated layout process transforms your role on the project, delivering significant value to the entire team. Framers using Dusty report several key benefits:
- Productivity: With the GC’s support, automated layout sets your crew up for peak efficiency. That means fewer hours on the job, lower costs, and higher progress billings.
- Fewer defects: Accurate layout of exactly what’s in the model ensures your work—and the work of downline trades—is spot-on.
- Improved coordination: Automated layout turns the jobsite floor into the ultimate shared document, enhancing clarity and reducing conflicts. Truebeck Construction experienced this on a life sciences project. Andrea Hernando, Senior Construction Tech Innovation Engineer, explained: “With Dusty we’re able to have everybody work together and we can see if there are issues with layout points in the CAD before we lay them out in the field.”
When framers present the benefits of automated layout effectively, GCs get excited about its potential. With their support, you’ll streamline your process and add measurable value to the project. Read more about how to leverage that support once you have it.