Dusty for Industrial Automation
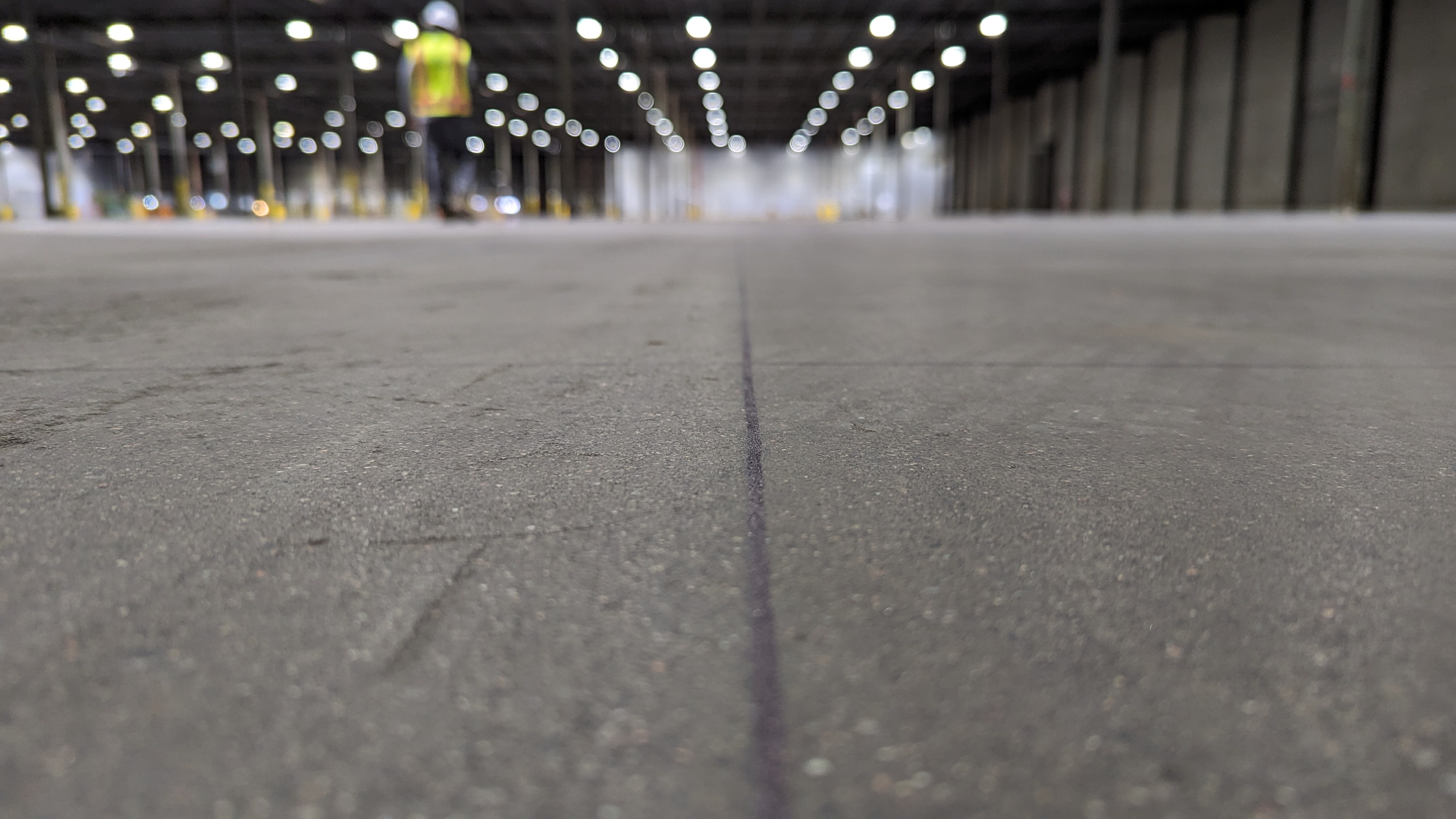
First, we got ourselves kicked off the construction site. Then, they signed a 7-figure enterprise contract. Here's how we did it.
It was the fall of 2022. An industrial automation company reached out to us with interest in our automated layout solution because they had a problem: they install robotic automation in distribution centers for global retailers, and they needed to mark out where miles of machinery and product shelving were to be installed with millimeter precision.
Traditional layout is labor intensive and takes months. They didn't have months, because the holiday shopping season was fast approaching and they had committed to being up and running quickly. In any manual process, human errors cause delays and extra cost. Each day these warehouses are not in operation puts these retailers’ revenue at risk.
Cue Dusty Robotics FieldPrinter. The project manager had heard of a robotic solution for layout, and wanted to know more.
I almost didn't take the call. At the time, robotic warehouse automation was not part of our ICP. Luckily my team took the meeting. The automation company was intrigued, and we agreed to a pilot on their next build-out.
The project team was excited. Our customer success manager, Nate, started training their operator. It went fast and the robot started printing points at our usual rapid clip.
The site team was amazed. “This is the future of layout for sure,” the PM said. Everyone was patting each other on the back, excited to be part of this momentous occasion.
Until: a problem. Anchor bolt locations were printed on top of a reinforced concrete pad that would support heavy machinery. The facility had been carefully designed -- and no anchor bolts landed on those pads. “Shut it down!” the superintendent yelled.
It looked like Dusty had made a mistake, casting into question everything that had been printed. The field crews started cursing out poor Nate, in both English and Spanish. He was told to leave and not return.
Our customer success team quickly convened online. Robots don’t make mistakes. It was probably an error in the model. Sure enough, the concrete pad was incorrectly modeled. One of the multiple different subcontractors had followed the model, but the model was wrong. When the concrete pad was overlaid on top of the anchor bolts, they overlapped -- which is exactly what Dusty showed in the field.
Once everyone calmed down, it was clear that the model was at fault, not the robot. The project team wouldn’t have discovered this bust for weeks using manual layout. We were asked to re-mobilize on the next warehouse build for a fresh attempt. The second trial, and the third, went perfectly.
The client was sold. In fact, because of Dusty’s accuracy, they gained a certainty they had never had before in the correctness of the model and how that translated out to the field. Rather than wasting time figuring out who made a mistake, they could rest assured that everything would be put in the right place.
Convinced that Dusty would be an integral part of all their upcoming warehouse build-outs, they inked a 7-figure enterprise contract for multiple robots deployed over the next three years.
Since then, we’ve helped multiple industrial automation customers bring facilities online sooner by getting all their trades collaborating on the same single source of truth.
If you would like to see what Dusty can do for your projects, we’d love to hear from you.