Understanding Control in Construction Layout: Methods, Pros, and Cons
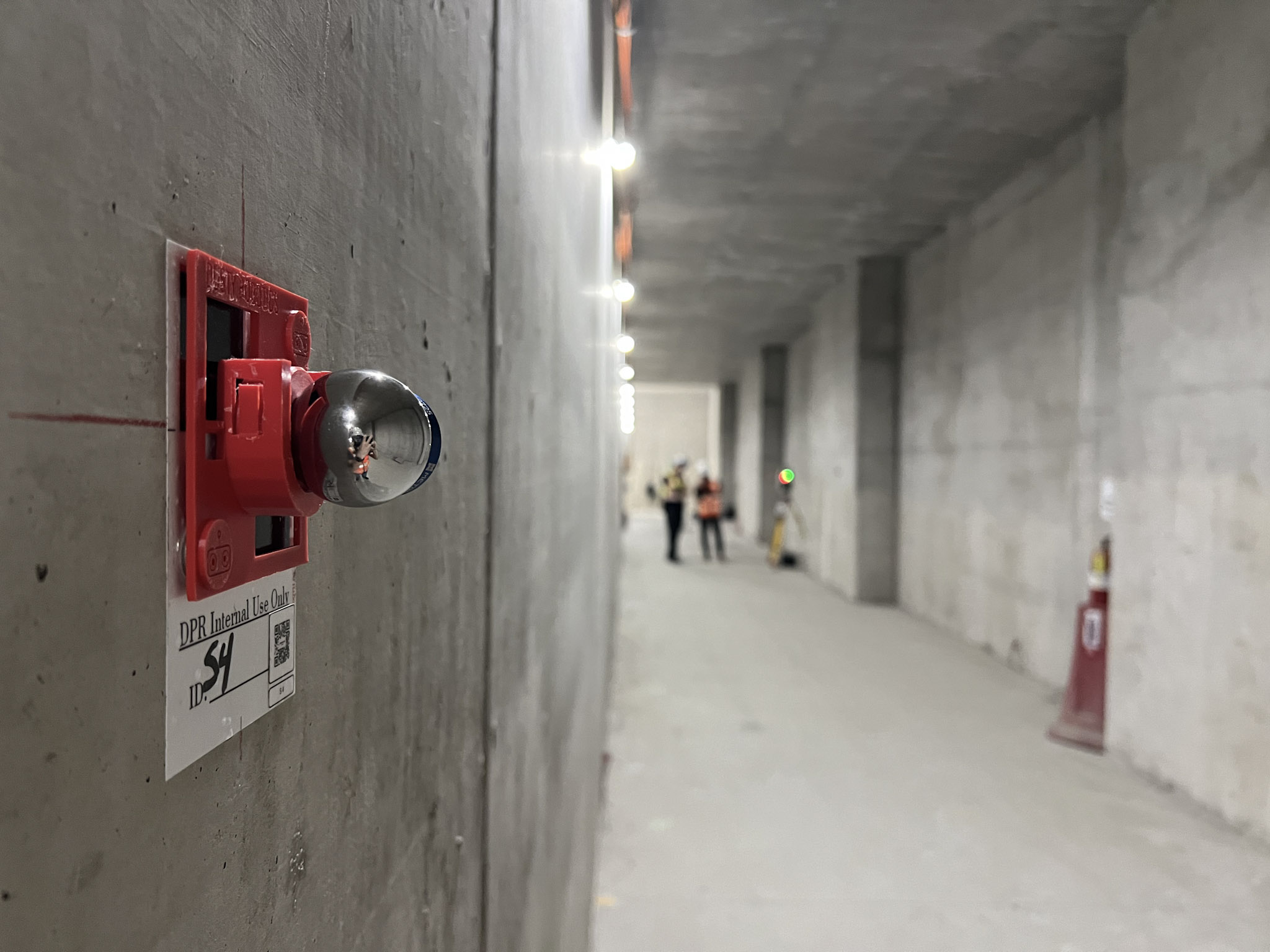
➜ This article is for you if you’re a a field leader considering automated layout but unsure how to adapt your existing control processes to new workflows.
In construction, control is the foundation of accuracy. It consists of a network of precise reference points that align a digital layout file with the real-world jobsite. Without a well-established control system, misalignment can cause costly errors, delays, and rework.
There are several ways to set control, each with different trade-offs in terms of accuracy, cost, time, and workflow adaptation. Choosing the right method depends on the needs of the project, the familiarity of the team with surveying techniques, and the level of precision required.
Why Does Control Matter?
Before automated layout products like Dusty Robotics FieldPrinter can begin their work, control must be established. Whether it's done manually with tape measures or digitally using advanced 3D scanning, the method of control impacts:
- Accuracy: Poor control can lead to cascading errors that affect the entire project.
- Efficiency: The faster and easier it is to establish control, the sooner layout work can begin.
- Collaboration: A common control network allows multiple teams and trades to align their work without conflicts.
- Risk Management: The wrong control method can introduce human errors or inconsistencies between stationings.
Automated layout requires a minimum of three control points inputted into the FieldPrint Platform at any one time, however you will have improved layout accuracy if you use more points. If you only use three points, it limits error correction—if one is off, the entire layout can be skewed. Additional points averages out discrepancies, reduces layout drift, and ensures alignment with the global control network. This prevents "blind spots" and maintains layout precision across the jobsite.
Let’s explore the six primary ways control is set on construction jobsites and how each method balances accuracy, efficiency, and cost.
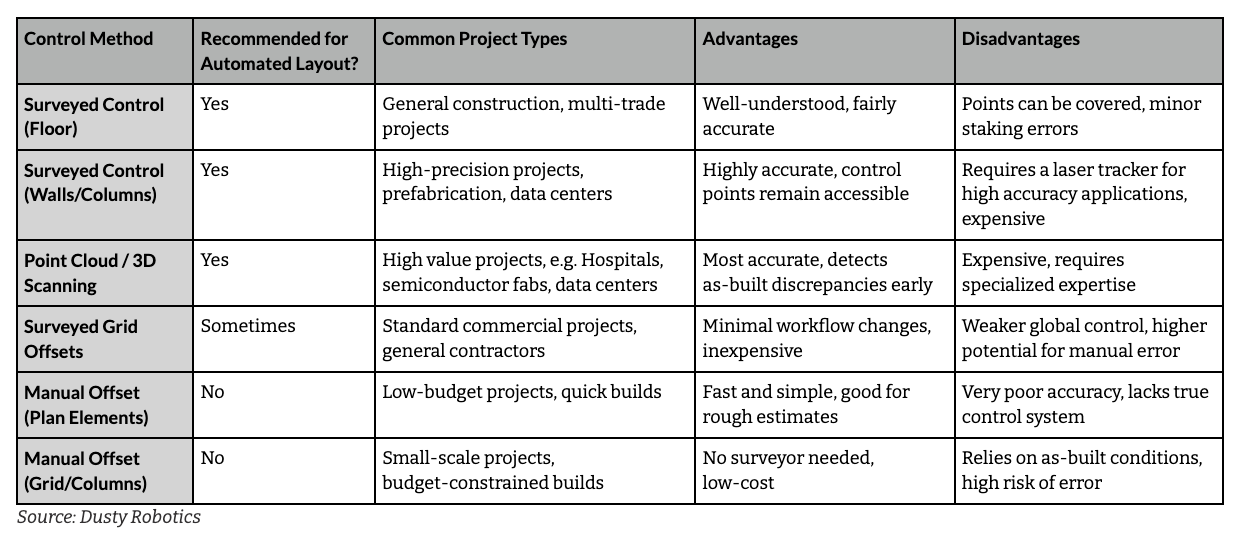
Surveyed Control on the Floor: The Most Common Approach
Placing control points directly on the floor of a construction site is one of the most widely trusted control methods. A survey team uses a Robotic Total Station (RTS) to mark precise control points based on existing surveyed elements. These control points are then used to align the digital layout to the physical jobsite.
This method is effective for most projects because it provides a good balance of accuracy, familiarity, and simplicity. Most surveyors are comfortable establishing control this way, and it creates a global network of points that multiple teams can use for coordination. However, since points are physically marked on the floor, they can be covered by debris or jobsite activity, making them harder to reference as construction progresses. Additionally, the process of staking points manually with an RTS introduces some degree of error, often ranging from ⅛” to ¼”.
Despite these drawbacks, floor-based surveyed control remains the most common approach due to its accessibility and practicality, and is most commonly used with automated layout.
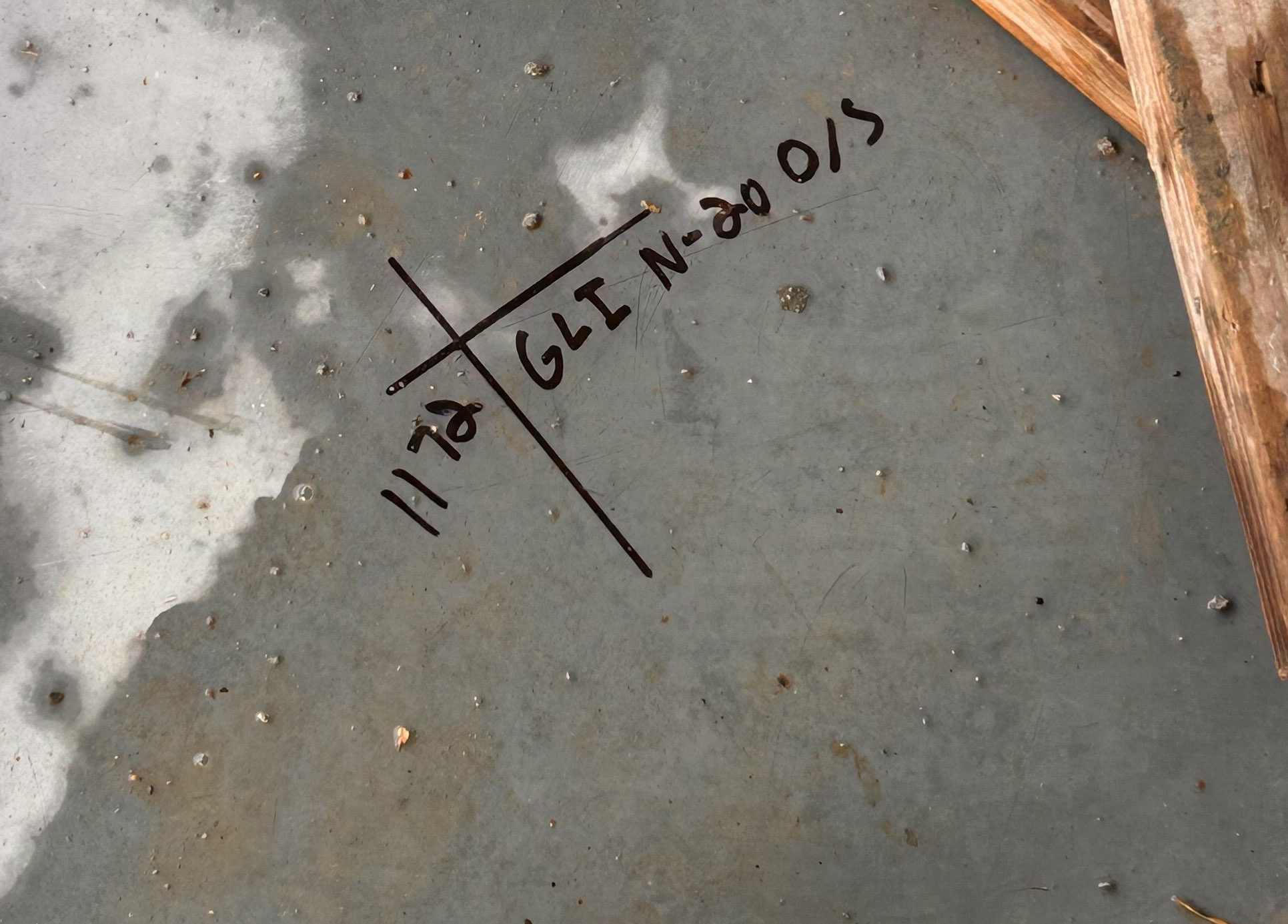
Surveyed Control on Walls or Columns: Highly Accurate Control
For projects where precision is critical, such as automated industrial applications like warehousing and manufacturing, or mission-critical prefabricated construction, wall-based control offers a major advantage over traditional floor-based methods in speed, accuracy, and precision. With the increased demand for wall-mounted control in construction layout, Dusty Robotics has developed a hybrid drift nest/target which allows for precise alignment by placing the drift nest over an existing target or mark alongside technology like 3D scanners and reality capture devices. This ensures accurate reflector placement and allows the Dusty FieldPrint Platform to be used in more field conditions and applications.
The approach to establishing control on vertical surfaces varies depending on the project type:
- Traditional Construction Sites: These projects are often well-prepared with control points already established on walls or columns at elevated locations. A surveyor mounts semi-permanent drift nests (magnetic holders for reflectors) onto the vertical surfaces and records their positions using a robotic total station (RTS) or a laser tracker. If these points are recorded using an RTS, their digital locations are adjusted to account for Dusty Robotics' wall control target offset of 1.25 inches.
- Industrial Manufacturing & Warehousing: In these environments, control targets are not pre-established, and surveyors create new points by affixing drift nests in strategic locations and tie them back to the digital layout with a laser tracker to precisely record their positions.
This approach is highly accurate, keeping station-to-station layout perfectly aligned. Unlike floor control, there’s no need to get on your hands and knees to ensure the target is placed perfectly on top of the mark, making the setup-to-layout time faster and more efficient. Depending on the project requirements, advanced equipment and expertise may be necessary, which increases costs. Additionally, it may require a significant change in workflow for teams that aren’t accustomed to working with laser trackers.
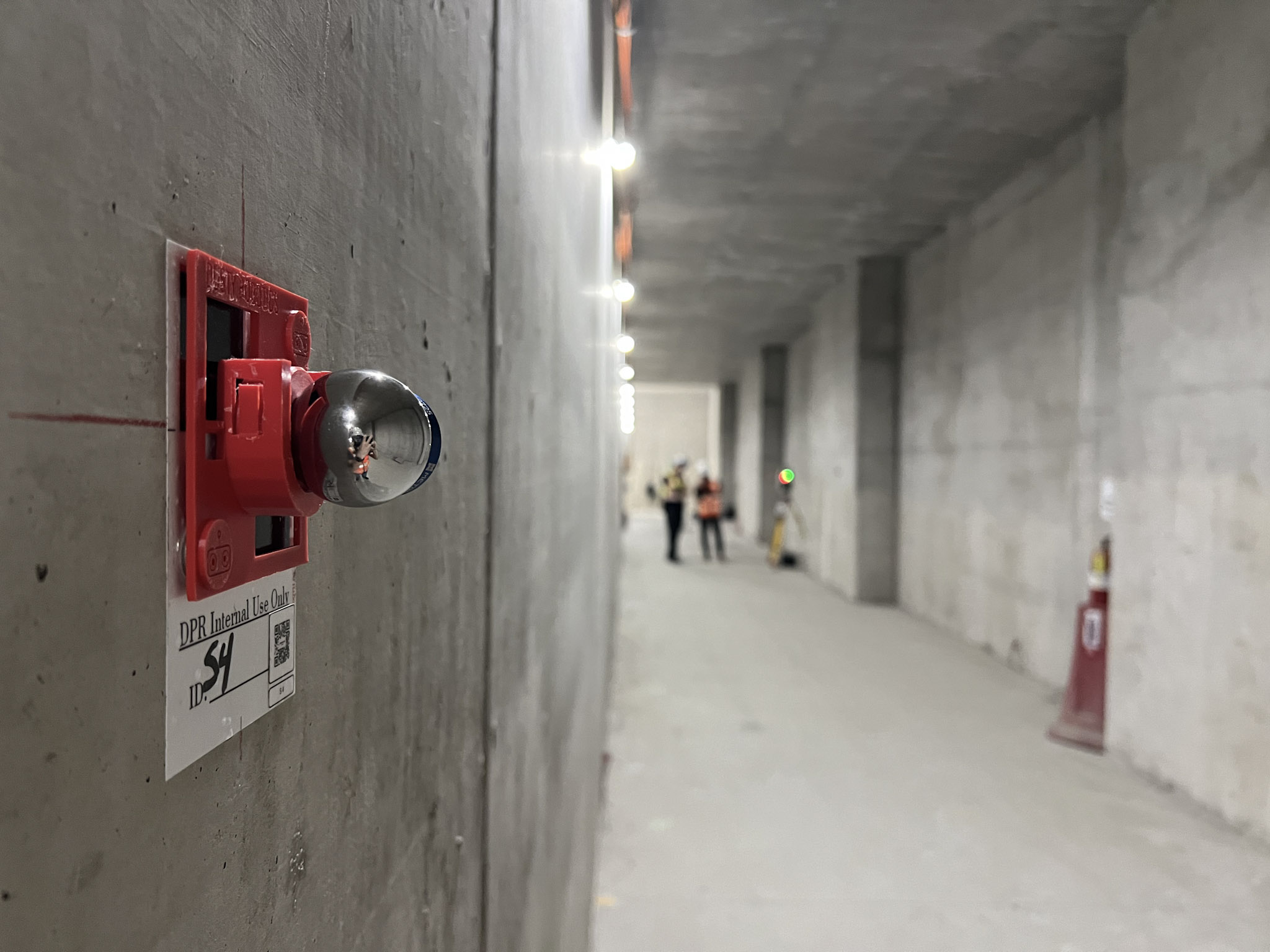
Point Cloud / 3D Scanning: The Future of Control?
Point cloud scanning is the cutting edge of construction control. It offers unparalleled accuracy by capturing as-built conditions in real-time. Using 3D laser scanners, teams generate a digital representation of the jobsite, from which they can extract precise control points.
The advantages of this method are clear: it identifies as-built discrepancies early, prevents layout errors before they happen, and allows for real-world field conditions to be integrated into the digital model by the VDC team. Additionally, point cloud data enhances collaboration between the field and office, ensuring that teams work with the most up-to-date site conditions.
This option allows the team the ultimate flexibility to place control points anywhere on the project. Control points can be placed before the scan with purpose-made targets that can be used solely for 3D scanning, or ones designed to be used with total stations have a prismatic reflector at the center point and can be recorded with a RTS. If as-built elements are well-captured in the 3D scan, physical measurement can be used to produce a point manually and recreate it in the digital layout.
This approach, however, requires specialized scanning equipment and expertise, making it one of the most difficult to coordinate and communication-intensive options. While it provides a high level of accuracy, it requires a commitment to coordination and data processing.
For large-scale, high-value projects—such as hospitals, semiconductor fabs, and complex renovations—3D scanning in conjunction with control is rapidly becoming the gold standard.
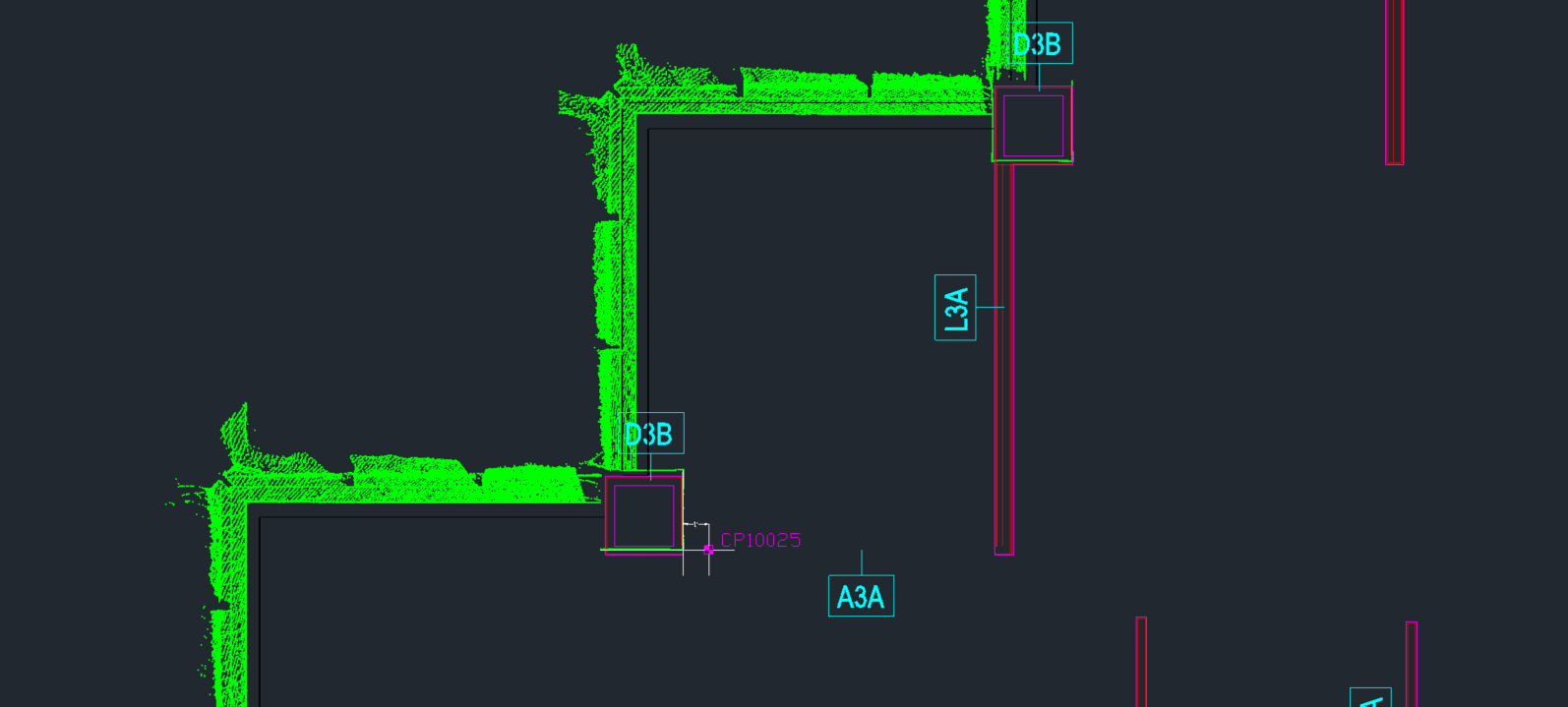
Surveyed Grid Offsets (Control Lines): A Transitional Approach
Many general contractors and layout techs are already familiar with grid offsets, making this method an easy transition to automated layout from traditional manual layout workflows. Instead of marking a series of discrete control points, a surveyor snaps chalk lines to establish offset control lines based on an existing reference grid. These intersecting lines create points that can be used for digital layout files.
The biggest advantage of this method is that it requires little workflow change, making it appealing for companies who are ready to move away from manual layout but need a crawl-walk-run transition plan into automated layout. Additionally, it is less expensive than full control networks and requires minimal communication between the field and office.
However, the trade-off is reduced accuracy. Unlike a precise network of building control points, offset lines have more potential for human error, and the global control network is weaker, meaning errors in one area can propagate throughout the project. This method works well for contractors transitioning to digital layout, but it lacks the precision of surveyed floor or wall control.
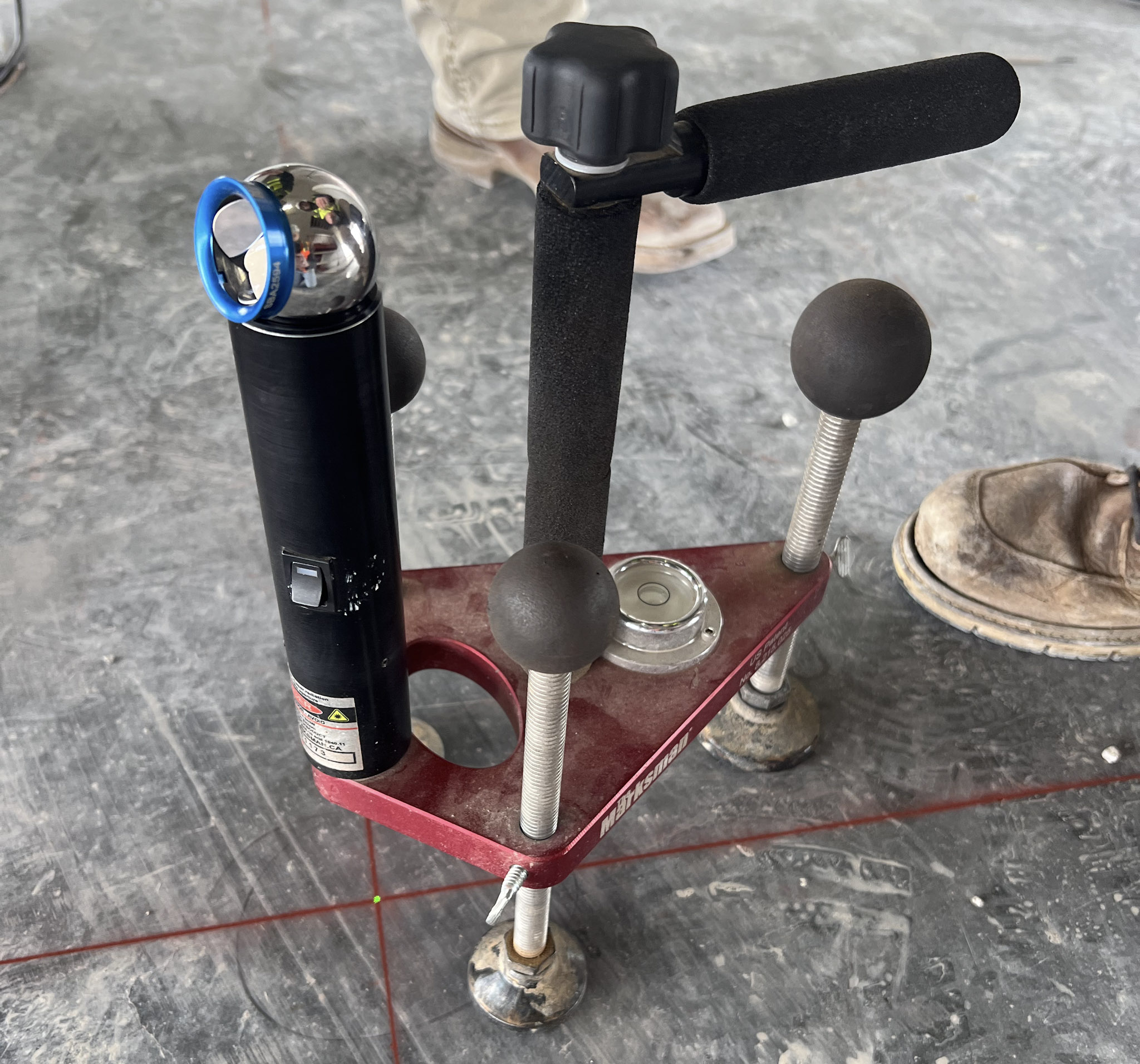
Manual Offset from Grid or Columns: Less Accurate or Reliable
For projects operating on tight budgets, some teams rely on manual offset methods, using existing building features—such as grid lines from column centerlines—to establish control points. This approach eliminates the need for a surveyor, as layout techs measure offsets themselves using a tape measure and chalk line to create intersection points, same as with Surveyed Grid Offsets (Control Lines) above
While this method is cost-effective and familiar to many layout professionals, it comes with major risks. It assumes that as-built columns are perfectly placed, which is often not the case. Without a verified control network, minor discrepancies can add up over long distances, leading to misalignment between trades. Additionally, human error is a constant factor, and there is no shared control system across different teams.
For small-scale projects or those where precision is not critical, manual offset can be a workable solution. However, for larger or more complex builds, the risk of error outweighs the cost savings, and it is not recommended with automated robotic layout.
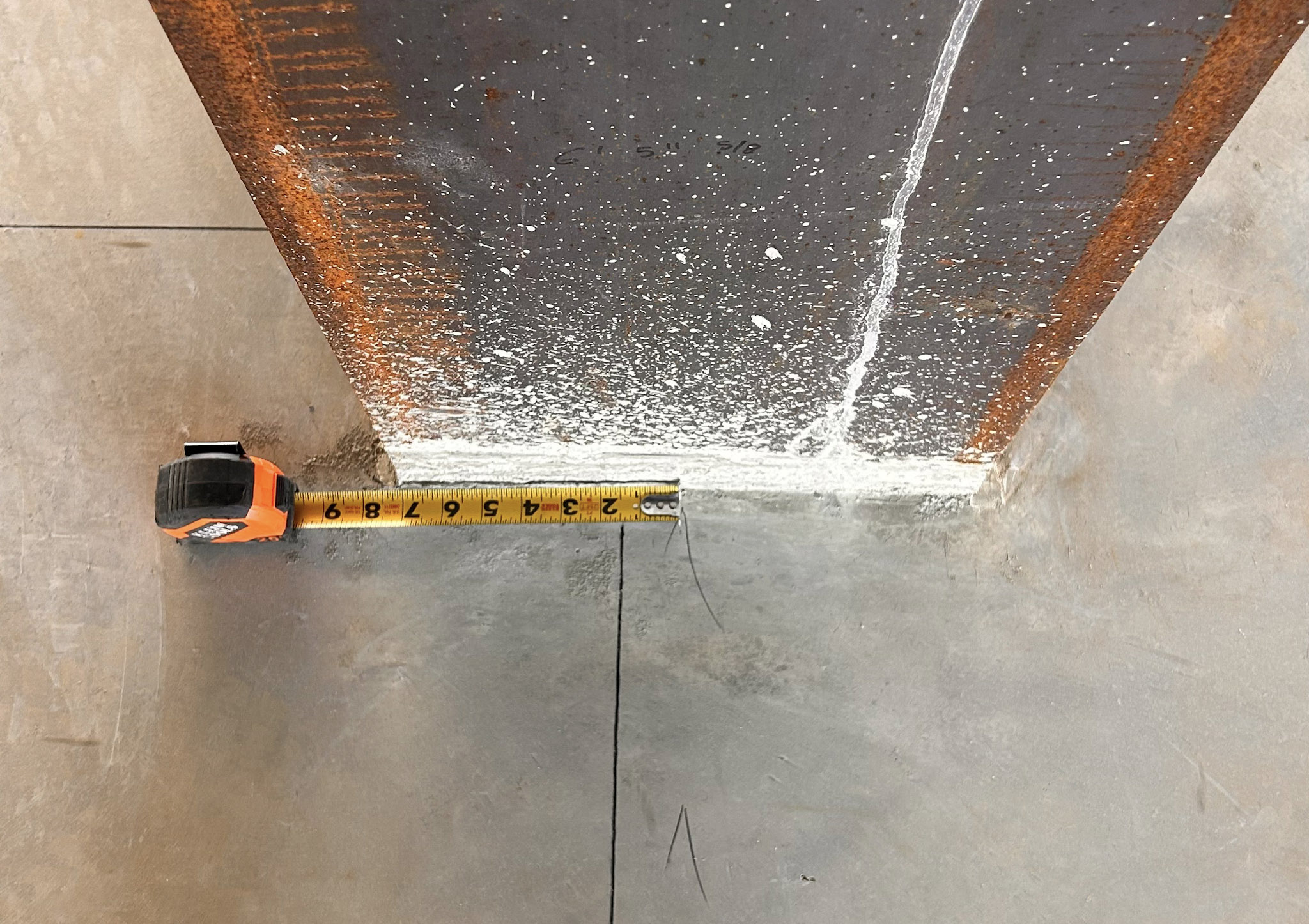
Manual Offset from Plan Elements: When Precise Control Isn’t Needed
Another low-cost control method involves measuring offsets from physical plan elements, such as slab edges, stair openings, or foundation corners. This method relies on field teams manually measuring offsets and transferring them into the digital layout file.
This approach has the same cost-saving benefits as manual grid offsets, but it relies even more heavily on as-built accuracy. Any discrepancies in slab placement or column positioning will directly affect the quality of the control network. While this method can provide insight into whether as-built conditions match the model, it lacks the reliability of a true control system.
For teams looking to verify existing conditions but not necessarily establish precise control, manual plan offsets can be useful. However, it’s not an ideal long-term solution for high-accuracy construction.
Choosing the Right Control Method
With so many ways to establish control, there’s no one-size-fits-all solution. Instead, contractors must weigh several factors to determine the option that best aligns with the project needs, budget, and their comfort of adoption:
- Project Complexity: High-precision projects benefit from surveyed control or point cloud data.
- Budget Constraints: Manual offset methods are cheaper but less accurate.
- Workflow Familiarity: Aligning with existing workflows minimizes resistance to change.
- Collaboration Needs: A common control network improves multi-trade coordination.
At Dusty Robotics, we work with all these control methods to streamline layout automation. No matter which method a contractor chooses, our system ensures precise alignment, reducing errors and rework.
If you're interested in seeing how Dusty Robotics can fit into your workflow, contact us for a demo and experience the benefits of automated layout.
Let’s Talk!
Which control method do you currently use on your projects? Have you considered upgrading to a more precise workflow with automated layout? We’d love to help you get started.