Alston Construction is a top 50 ENR general contractor that operates in 23 locations across the United States. Alongside its Automation Integration Management (AIM) team, Alston was contracted by the owners of a cutting-edge robotics warehouse and distribution center to turnover the second phase of a strategically planned three-phase installation where the most difficult task was tying into the first phase of the installation which was completed a year prior with less than precise layout equipment. Alston was asked to include automated layout as a core component of the project directly by the project owner in order to achieve the accuracy and speed required on this complex job.
Rickey Molina, VDC Director for Alston Construction, explained that “We had a very condensed and convoluted area to work in inside the existing space while maintaining a fully operational distribution center at the same time. The AI-powered robotic automation that the client deals with is very complex, very precise. So older or traditional methods of layout and installation just weren't gonna cut it with the 1/16th inch or better accuracy that we needed on this jobsite.”
In order to achieve these results, Alston Construction partnered with ENG BIM for its hands-on production BIM services, including the translation of the full digital model to what was needed in the field.
Maria Diaz, BIM Coordinator for ENG BIM, knew that “the client produced a lot of critical information during the design phase, but in some prior projects, that was not being translated to the field during the construction phase, impacting construction efficiency.”
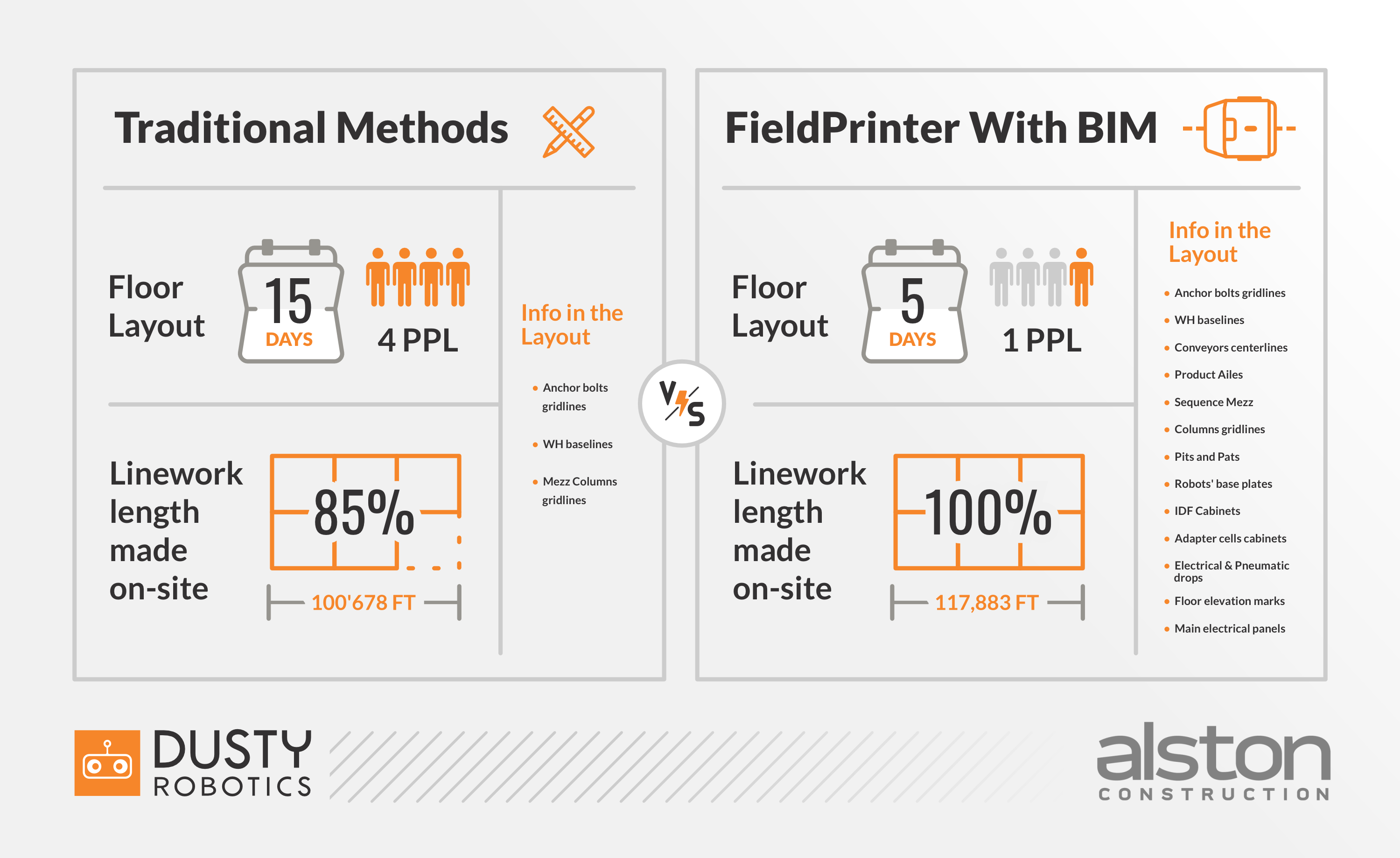
Speed and Accuracy Combined
To be effective on this jobsite, the Dusty Robotics system had to not only be accurate, it also had to be fast. Alston compared its overall layout performance on this project using Dusty Robotics versus similar prior projects, and found a staggering difference. What used to take a crew of four people 15 days – for a total of 60 person-days – now took a single person just five days to complete.
That means per person-hour, Dusty was 12x faster than total station-based layout!
Accuracy was critical on this project. Molina explained that “Our client designed an amazing new system with these robots moving up to 25 miles per hour. But in order for it to work, the offset between rails couldn’t be more than 1/16th of an inch. So this construction required high quality checks that were costing us time. With Dusty, we could maintain a 16th of an inch precision across the entire jobsite.”
At first, everyone wanted to verify accuracy manually with traditional methods, but as the project went on, Molina heard from his team that “each time we checked manually, everything was right on, and that really gave people the confidence to trust in the layout going forward – the results spoke for themselves.”
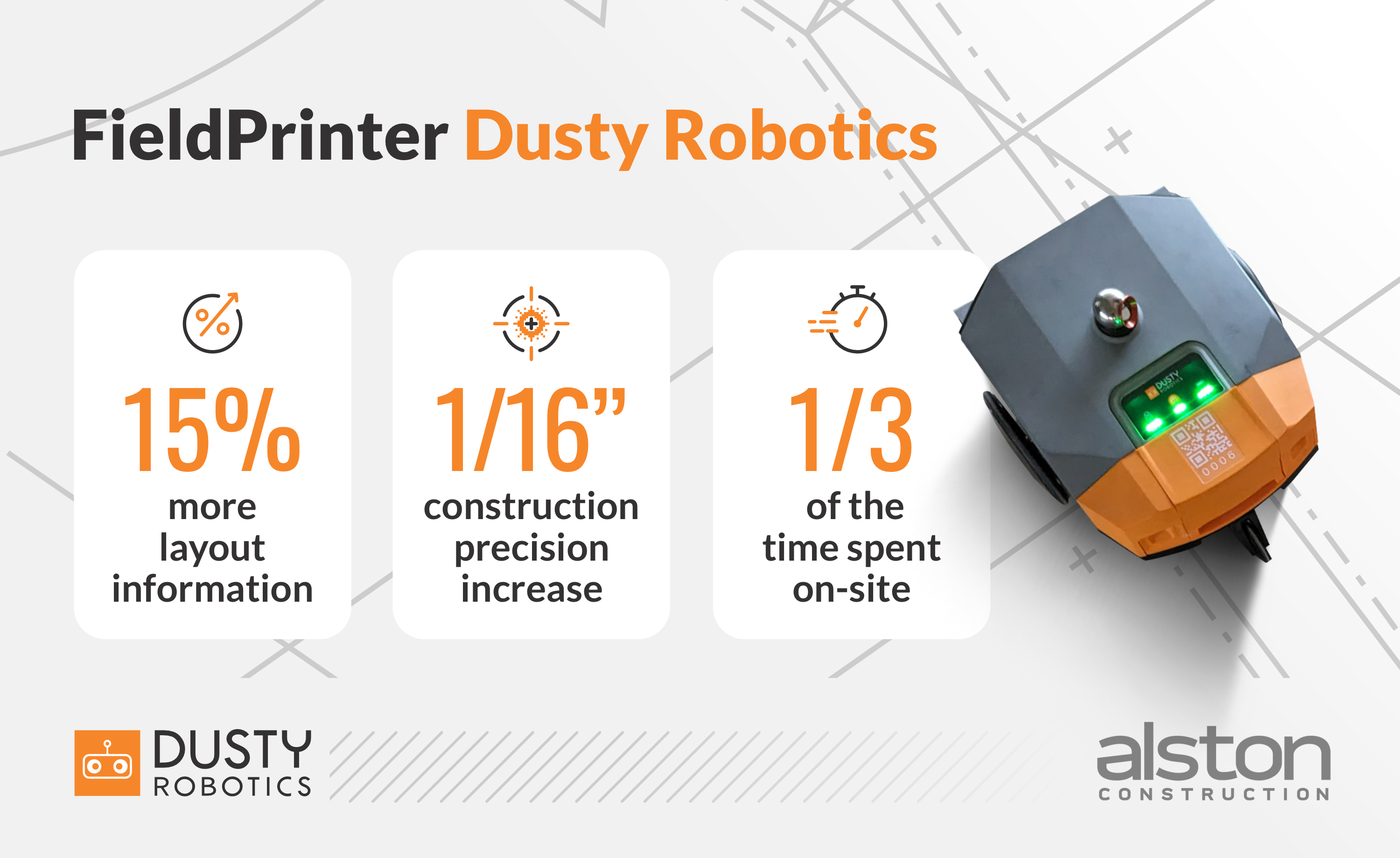
Additional Details Included as Part of the Layout Process
The Alston team knew that it wasn’t just about getting the same type of layout they’ve done in the past – it was also about including additional information that wasn’t available during the course of construction in the past. In previous layouts, they laid out core elements – anchor bolt gridlines,datum lines, and column gridlines. With Dusty, that expanded dramatically – and included all of that plus new elements such as conveyor centerlines, IDF cabinets, electrical and pneumatic drops, and much more. Molina explained that “there was a whole plethora of information that was encompassed in our layout file and we're able to print all of that, and then all of this while maintaining that sixteenth of an inch needed precision on site.”
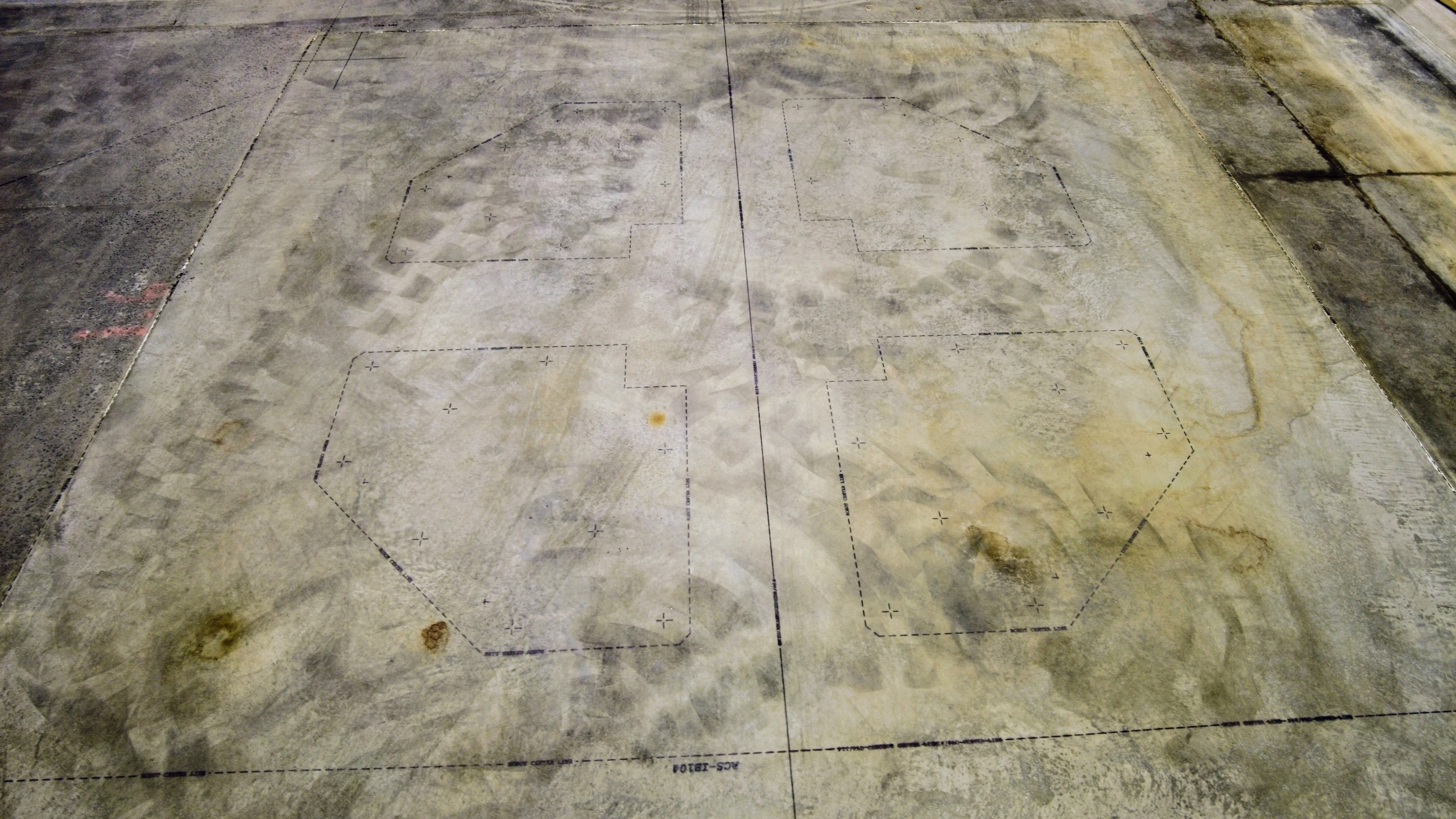
The FieldPrinter system also provided additional information to the team about overlooked errors from the model or from manual layout, so that even the smallest inconsistencies can be recognized and corrected immediately.
Where new installations mate with existing systems not laid out with the FieldPrinter, more often than not, small adjustments to the new layout file need to be made in order for the systems to seamlessly connect together. Using the FieldPrinter, Alson was able to verify alignment to existing systems by checking critical tie-in dimensions and rapidly deploy adjustments to skew, or shift X and Y placement of any installations layout. All of which would otherwise take days to push through the design team for a fix and reissue drawings.
Ease of Use Remains Paramount
Even with all the advantages, the Dusty system had to be easy to use and aligned with existing business processes. In order to translate the digital models to the field, Diaz adapted her existing workflows by working hand-in-hand with the construction team to resolve any issues earlier in the process, and described the process as “the BIM team used Dusty’s solution to help bring the power of the model more directly into the field.”
Molina partnered closely with the operators of the system throughout the project, and said that “from the operator standpoint, the FieldPrinter was very easy to use, and that “the iPad app makes it simple to mark out obstacles – overall, Dusty makes it easy to adjust and move things around, and get the layout completed.”
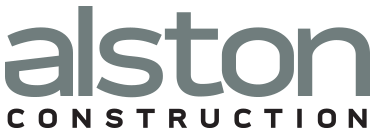
Alston Construction, a top 50 ENR general contractor, was contracted for the second of a three-phase turnover of a cutting-edge robotic warehouse and distribution center.
Interested in learning more about the
Dusty FieldPrinter?
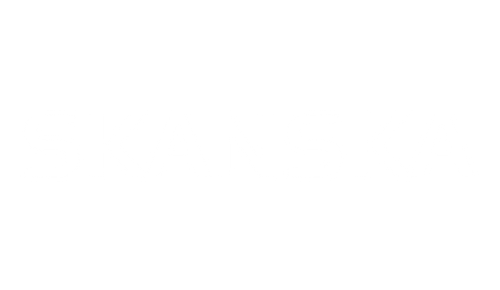
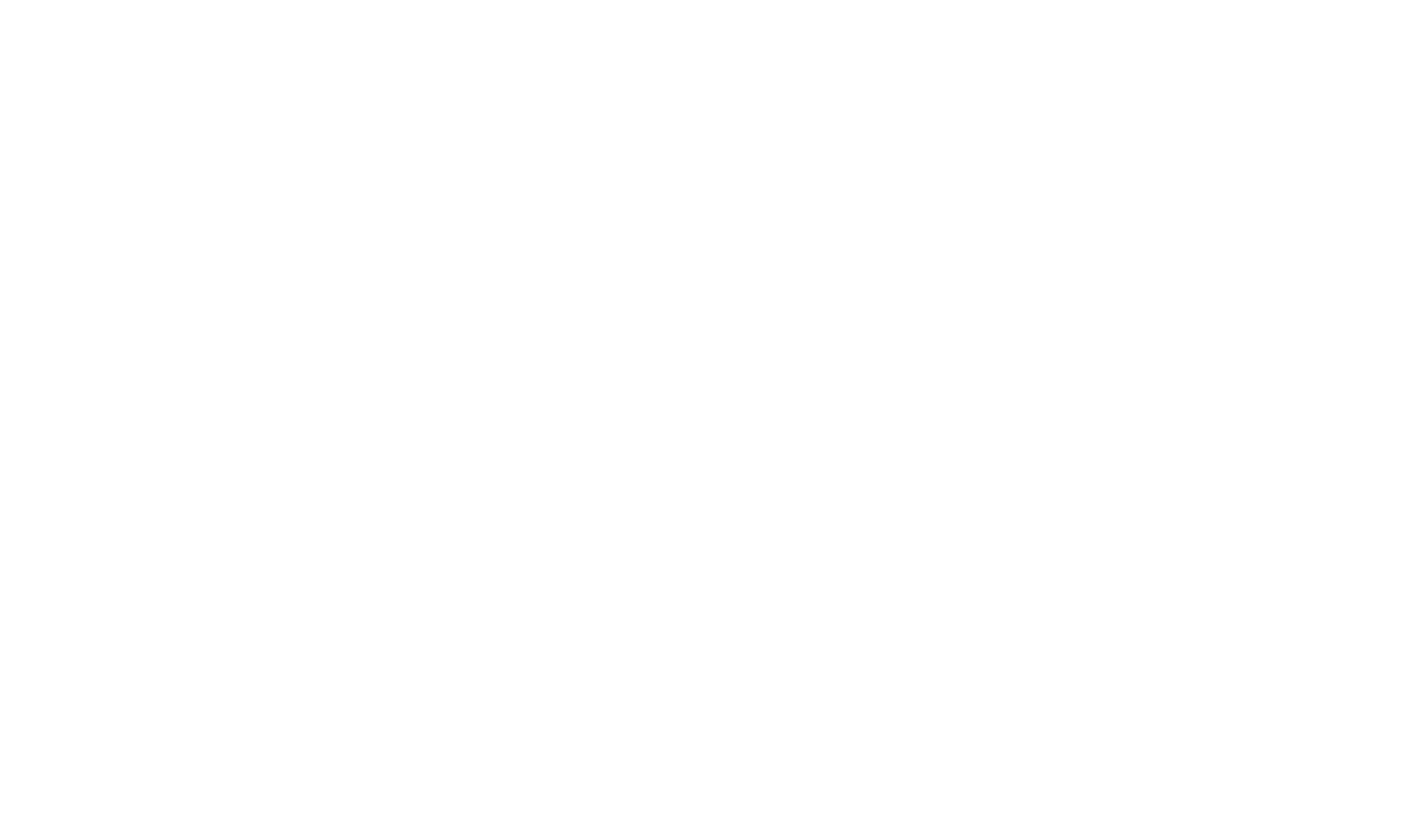
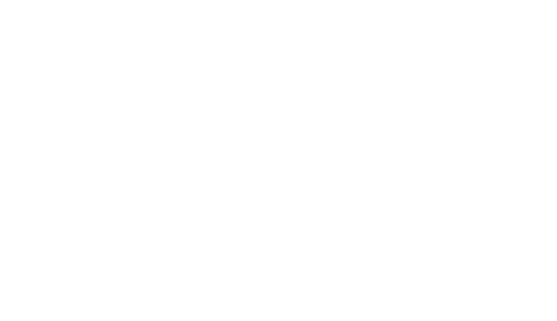
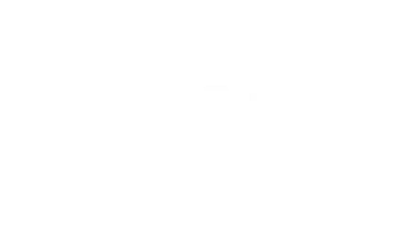
.png)
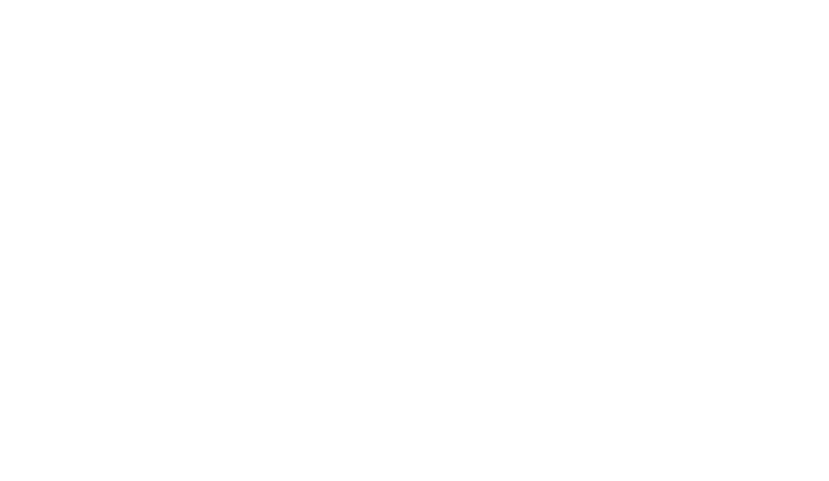