JE Dunn Coordinates Four Trades on The Knoxville Temple with Dusty Robotics
JE Dunn Construction is the eighth-largest domestic general contractor in the United States, with 26 offices nationwide and 100 years in the business. The company has established itself as a trusted partner for complex and high-profile projects, delivering excellence across a diverse range of sectors, from data centers and healthcare to religious institutions.
JE Dunn was the contractor for a new temple in collaboration with the Church’s Special Projects Department, which demands extraordinarily high standards of accuracy and quality due to its intricate design and detailed specifications.
Ambitious Quality Standards on a High-Profile Project
The high standards for the Church’s temples are meticulously outlined in their spec book, which compiles design standards, construction methods, and materials for all their projects. Jeff Lackey, Senior Superintendent at JE Dunn, has more than 30 years of experience in the construction industry. He says the Church’s spec book “reflects the church’s commitment to high standards and consistency across all of their temple builds.”
Dusty Robotics plays a key role in meeting the Church’s quality requirements.
"We chose Dusty Robotics for this project because it delivers the precision and efficiency needed to meet the high standards we want,” says Lackey. “Dusty’s technology enables faster, more accurate layout, helping us stay on schedule, reduce errors, and create a safer environment for our workers—all while meeting the tight tolerances and intricate design specifications that makes this project unique.”
By achieving these strict tolerances of 1/16 of an inch, Dusty Robotics helped to safeguard the overall construction schedule and the long-term success of the build.
“Dusty’s accuracy was key to achieving the level of finish we needed,” says Lackey. “Dusty’s layout was exactly as modeled, and we met the owner’s standards without the need for any corrective measures later in the process.”
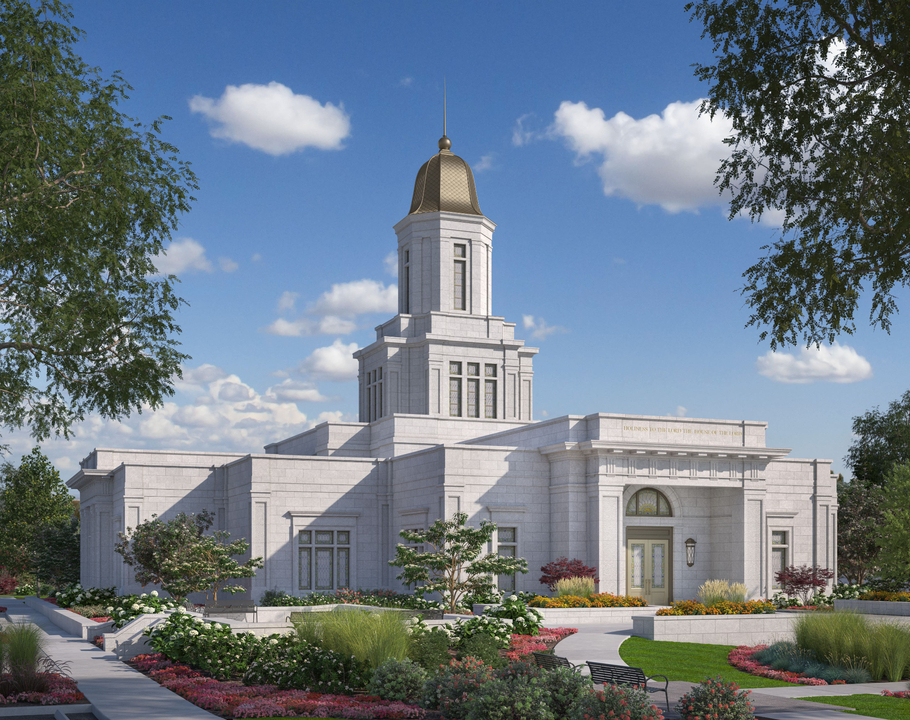
Coordination Across Four Trades with Dusty
JE Dunn’s previous experience with Dusty Robotics was highly positive, leading a JE Dunn team member to recommend it for this temple.
For the layout process, four key trades collaborated in a unified approach, moving away from the traditional method where each trade performs its own layout at different times using separate tools and independent control. This streamlined method quickly gained the support of the trades because it ensured the right people were using the right tools, yielding big schedule wins, and also eliminated the potential for coordination problems and manual layout errors. Each trade retained the responsibility to check and verify their layout for final accountability.
"Once we explained how Dusty had reduced errors on other projects and gave them assurance that each trade could verify the layout themselves, everyone was on board. The different trades all saw that automated layout is the best way to achieve accuracy and avoid mistakes on projects,” Lackey explains.
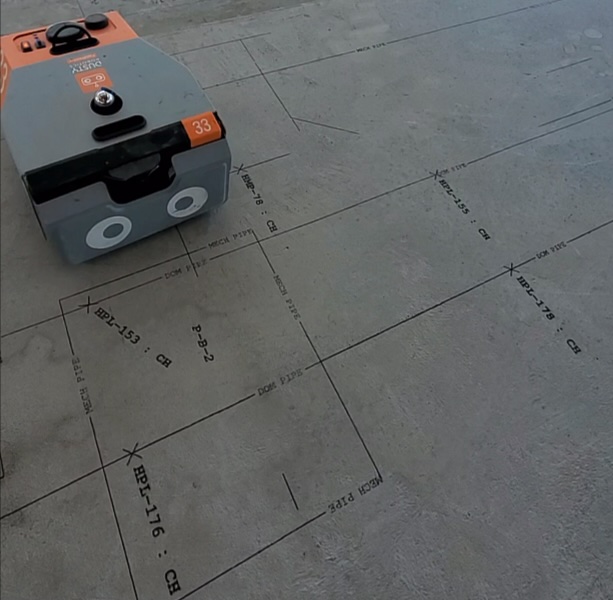
Bridging the Communication Gap Between Digital Design and On-Site Execution
Traditionally, after the VDC (Virtual Design and Construction) team federates and coordinates the BIM (Building Information Modeling) model, that information gets flattened into drawings, shipped to the jobsite, and selected information is laid out on the floor one trade at a time. Communication between VDC and field teams becomes sporadic and the field’s visibility to the rich information in the model becomes very low.
This helped break down the barrier between the field and the model.
Such consistent communication proved invaluable on the temple build. The continuous dialogue ensured that design discrepancies and existing conditions alike could be quickly addressed, preventing costly issues before they impacted the construction schedule. By integrating Dusty into the process, the team had the ability to discuss the layout regularly, adjust as needed, and ensure that the work stayed aligned with the design intent.
“Because Dusty has already laid it all out, if you notice an issue you have time to call up the architect before you're ready to frame an area and say, ‘This wall is not big enough. Can we widen this out? What is the plan?’” Lackey says.
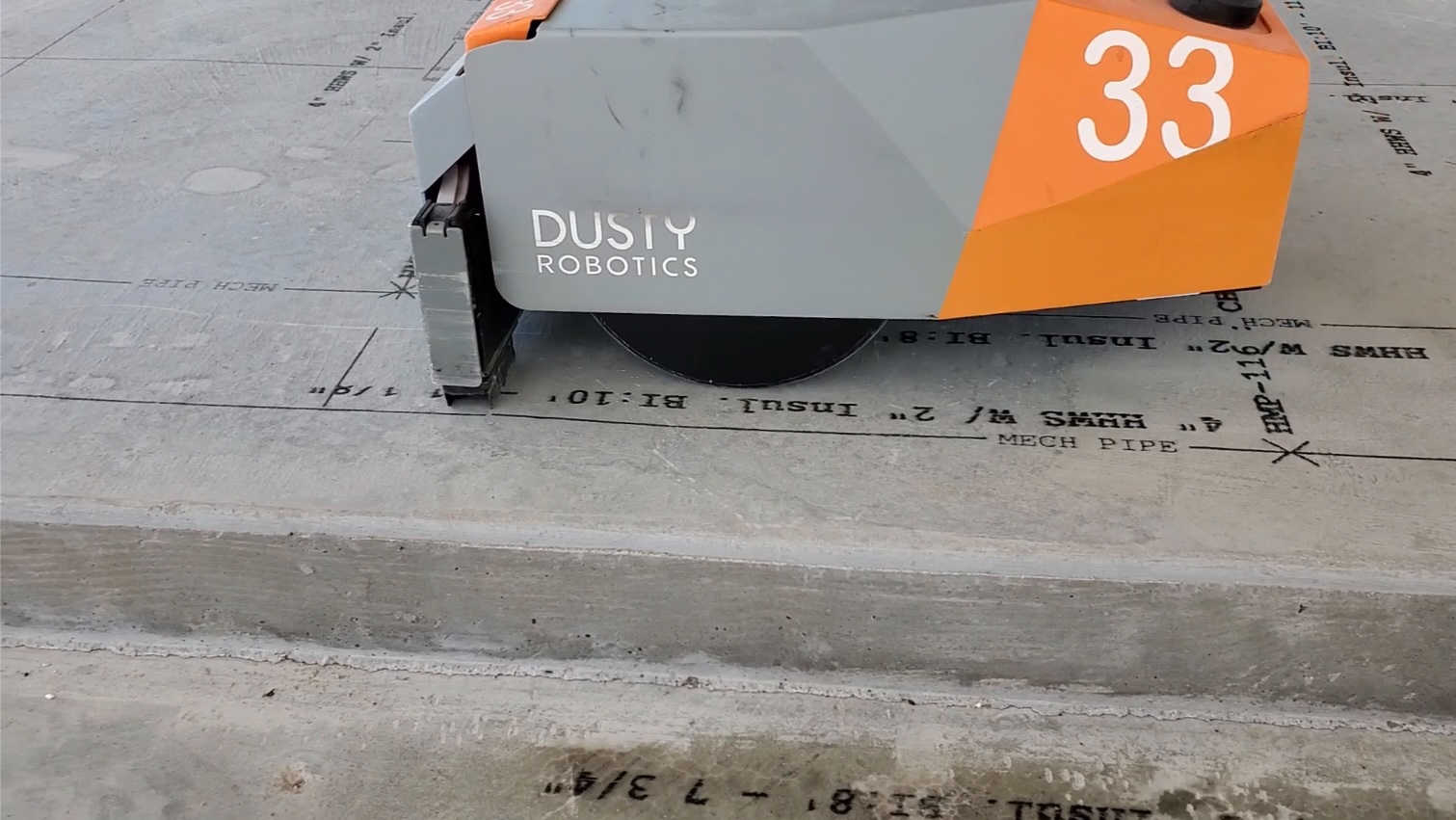
Fivefold Reduction in Layout Time
Dusty enabled JE Dunn to complete the layout in significantly less time, reducing a process that would typically require multiple field crew members more than two weeks to just a few days.
“Using Dusty Robotics, we were able to cut down the layout process from what would normally take 16 days with traditional methods to just three,” Lackey explained. “This fivefold reduction in time allowed us to move forward with the project more quickly while maintaining the highest standards of accuracy. It freed up valuable time for other tasks, ensuring we stayed on schedule and minimized delays.”
But the schedule wins didn’t stop there. Because JE Dunn used Dusty to lay out multiple trades at once, trade stacking became a lot more effective. Going beyond just walls, Dusty automated the placement of everything from pipes, to mechanical systems, conduits, and wall boxes—all in one step. Once Dusty completed layout in an area, everybody was able to get started, resulting in considerable efficiencies in the overall project schedule.
Reduced Rework with Faster RFI Processes
The efficiency of Dusty’s layout process allows for early identification of design discrepancies, reducing errors that would otherwise lead to costly rework. Dusty helps teams spot potential issues before they escalate, enabling proactive solutions.
With the information from the FieldPrint Platform, JE Dunn could quickly submit and resolve requests for information (RFIs) to not only keep the project on track but also ensure that no time was wasted in correcting mistakes later in the process.
“With Dusty, we were able to generate a question—and find an answer—much quicker,” says Lackey. “When we had a wall that was too small for the pipe, we got it resolved well before it was time to build the wall.”
By resolving issues earlier in the process, Dusty’s accuracy and speed helped keep the project moving smoothly and on schedule.
Enhanced Safety for Workers
Dusty Robotics also relieved workers from the physically taxing, backbreaking work of traditional layout, where bending or kneeling for extended periods is common. By automating the layout with Dusty, JE Dunn was able to keep workers off their knees, reducing strain and potential injury—an important improvement for on-site working conditions.
“It’s not just about saving time and accuracy; it’s about the ergonomics,” says Lackey. “These builders are no longer on their knees doing this layout. That’s a big part of it.”
Thanks to Dusty Robotics’ proven efficiency, time savings, and enhanced accuracy in the layout process, it’s now a go-to solution for JE Dunn projects.
“Dusty’s technology brings real solutions and coordination to the jobsite. Dusty’s technology helps us stay on schedule, reduce rework, and deliver high standards to our clients,” Lackey says. “With Dusty, we can tackle the most demanding projects with confidence, knowing that the layout is perfectly aligned with the design every step of the way.”
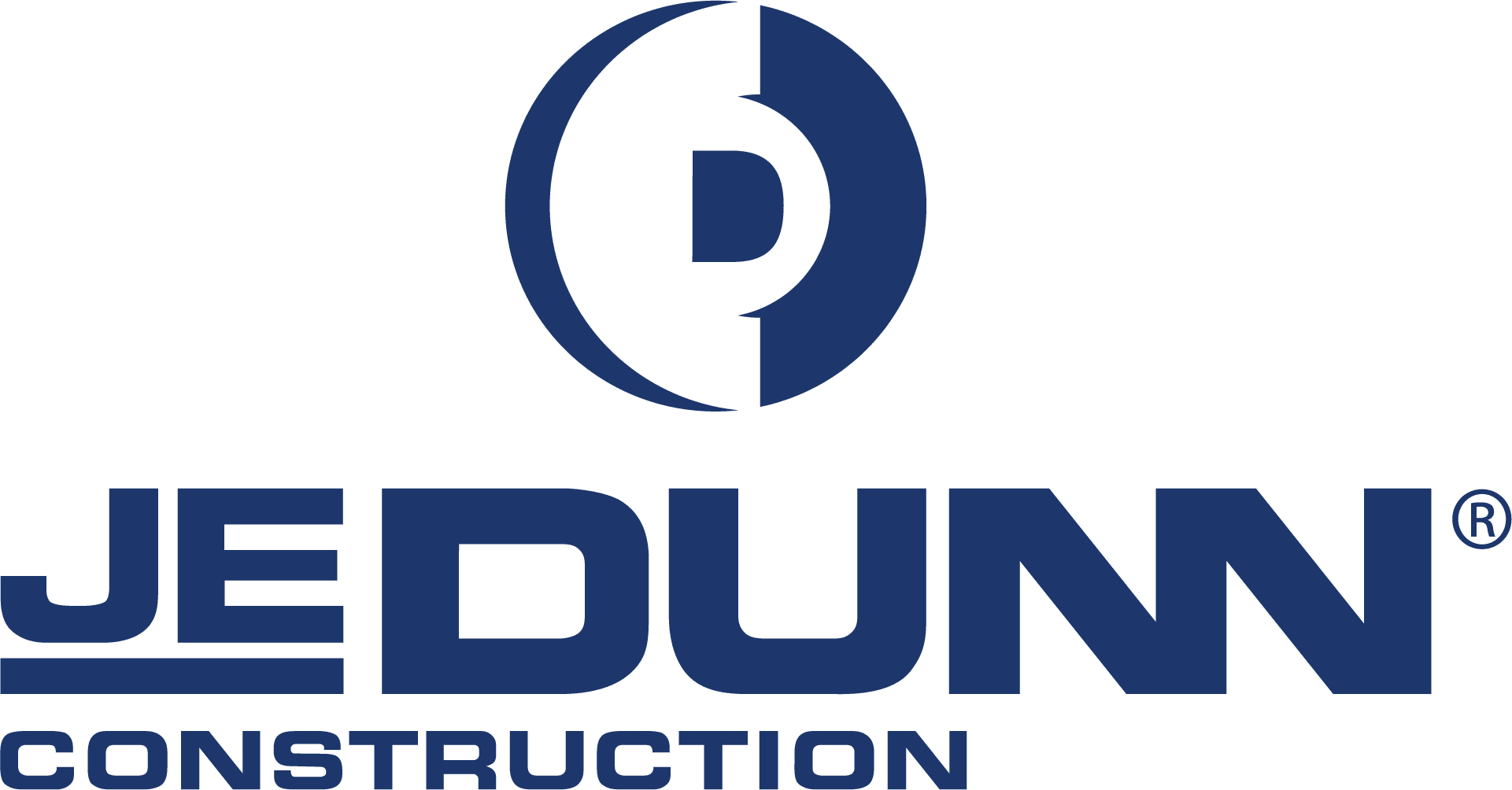
JE Dunn Construction built a high-profile temple for The Church of Jesus Christ of Latter-day Saints, with tight schedule constraints and high architectural ambitions. They chose Dusty Robotics as their multi-trade automated layout solution to streamline and accelerate the project's progress, coordinating for different trades while completing the layout 5X faster.
Interested in learning more about the
Dusty FieldPrinter?
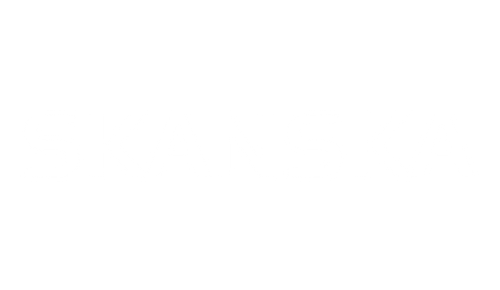
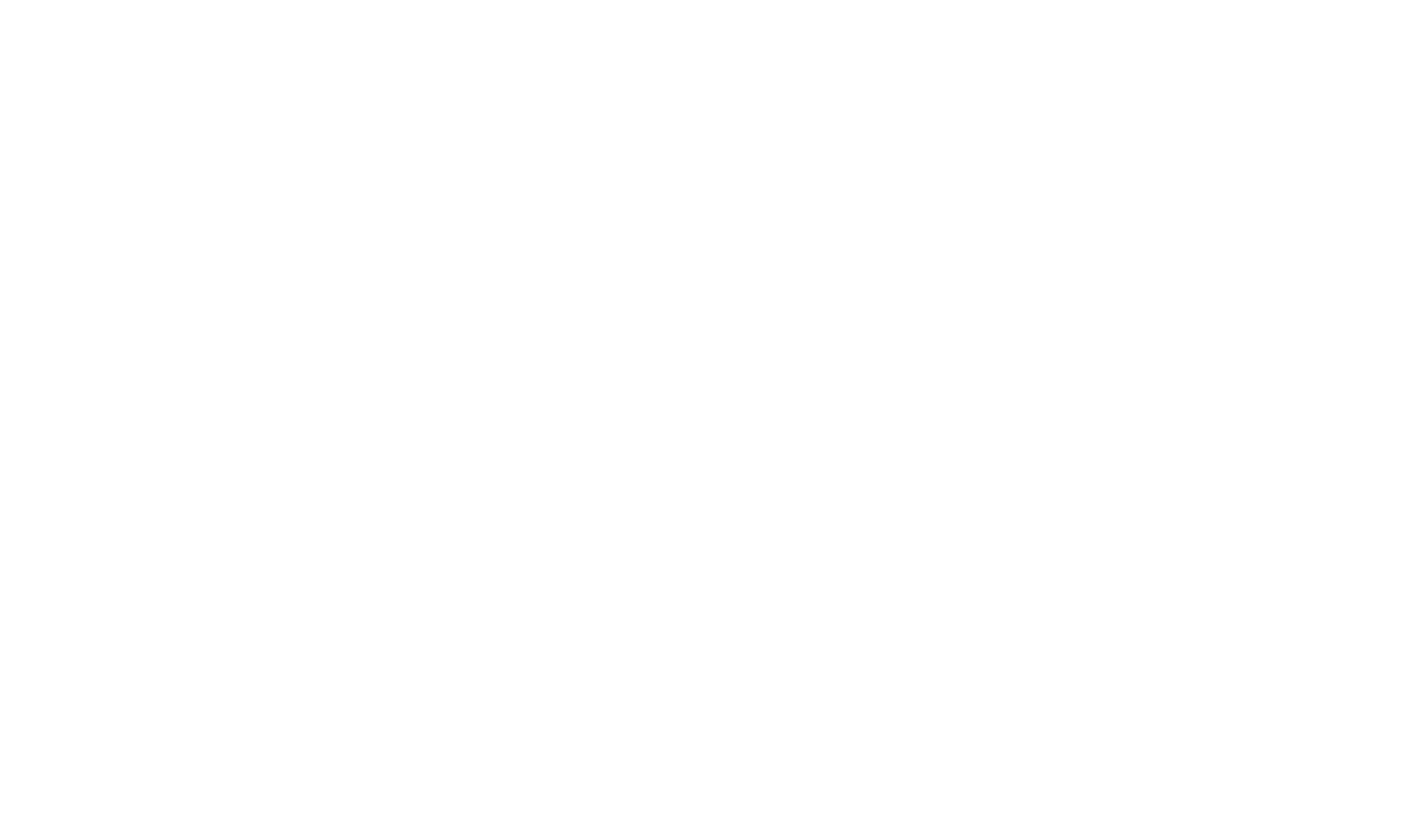
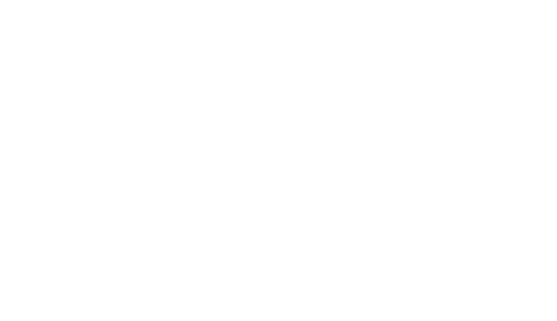
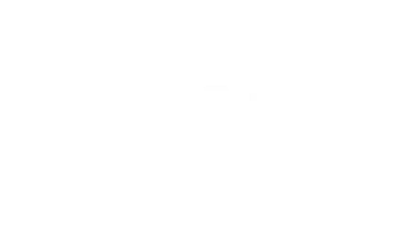
.png)
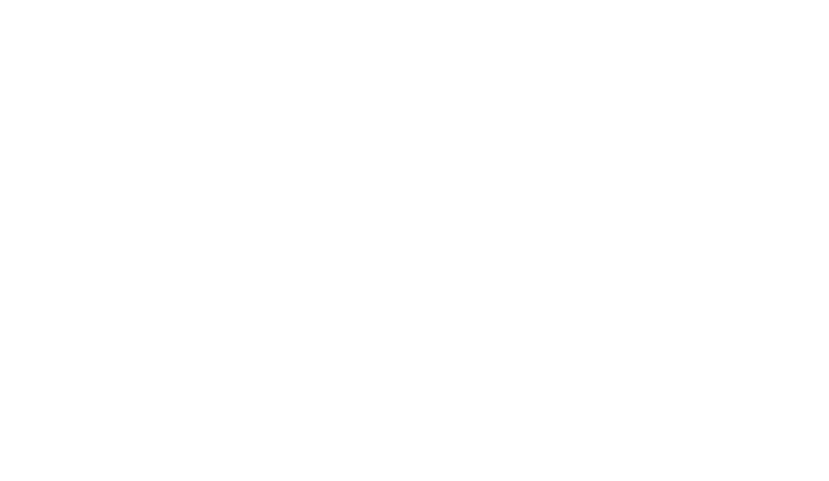