Complex Collaborative Design Translated Directly to Field with Robotic Layout
Once complete, the Kaiser Roseville Medical Center will be the largest hospital across all of Kaiser’s facilities–and overall in Placer County, California. What’s more, the hospital will bring hundreds of new jobs to the community and, according to Roseville Mayor Bruce Houdesheldt, “ensure that Roseville will remain a desirable place to live, work, and play.”
Leading the project is McCarthy, engaged by Kaiser to ensure the success of the high-stakes project. “The Roseville Kaiser hospital is one of the busiest in California,” said Glen (Sully) Sullivan, VDC Manager for McCarthy. “It's a community hospital in the foothills where there aren't as many choices. The need is so high.”
The $1B project includes a new 272,000-square-foot, six-floor hospital tower with 138 hospital beds and 36 emergency department beds and will provide structures for the latest innovations like surgical imaging & monitoring equipment, tele-critical capabilities, and technologies required to care for patients with complex needs.
To meet that need, Kaiser and McCarthy operated under an Integrated Project Delivery (IPD) contract in order to prioritize cross-trade collaboration from design to construction.
To bridge the gap between elaborate digital coordination and field execution, McCarthy turned to Dusty Robotics. “Dusty helped us adhere to our coordinated model and control risk,” said Zahel Gonzalez, Project Manager at McCarthy. “We’ve already built the project in our heads and in the model—with Dusty, we know it can be replicated exactly in the field.”
From the outset, McCarthy faced intense schedule pressure to complete the project on time. Dusty compressed the schedule in three key ways: reduced rework, faster layout execution, and more efficient construction processes.
McCarthy Mitigated Risk by Leading Multi-Trade Collaboration and Augmented Layout
When it came to the design and coordination effort, this wasn’t any ordinary project. To pack complex systems into constrained space, the team pushed the modeling effort to LOD 400. “We modeled every stud,” said Daniel Starr, VDC Senior Engineer at McCarthy, “and then we laid out each one with Dusty.” Gonzalez added, “we used Dusty to lay out thousands of additional points for additional clarity we would never consider including with manual layout.”
The headwall systems in each hospital bed was like “fitting fifty pounds of stuff into a five pound box,” Gonzalez quipped. Dusty became the vehicle for making sure McCarthy’s investment in the meticulously coordinated model bore returns in the field. “Dusty reduced confusion and made people spend less time trying to figure out what went where. It prevented the mistakes that cause rework, like the plumber using the electrical inserts.” Gonzalez continued, “McCarthy used Dusty to control the time risk of schedule delays and financial risk of cost overruns.”
“It’s hard measuring the mistakes that didn’t happen,” Gonzalez admits. But Starr noted that rework and manual layout went conspicuously hand-in-hand. “In the past, we had issues with work not matching up to shop drawings and what's been in the model,” he said. And Sullivan noted “on previous projects, there have been issues in the field where a trade didn’t install something correctly and we've had to address it, but with Dusty, there's a lot less risk in making sure that everything gets built correctly. On this job, everything was installed the way we intended it the first time.”
This type of change requires a partnership, both with all of the trades on the project and with Dusty. Performance Contracting Inc. (Framing), Morrow Meadows (Electrical), Frank M. Booth (Mechanical), and Pan Pacific Mechanical (Plumbing) all collaborated together on a single unified model and layout process. Gonzalez described the partnership with Dusty as, “the Dusty team is awesome. If we have any questions or need some additional training, the team is very quick to respond and walk us through the steps in the field or with the design team.”
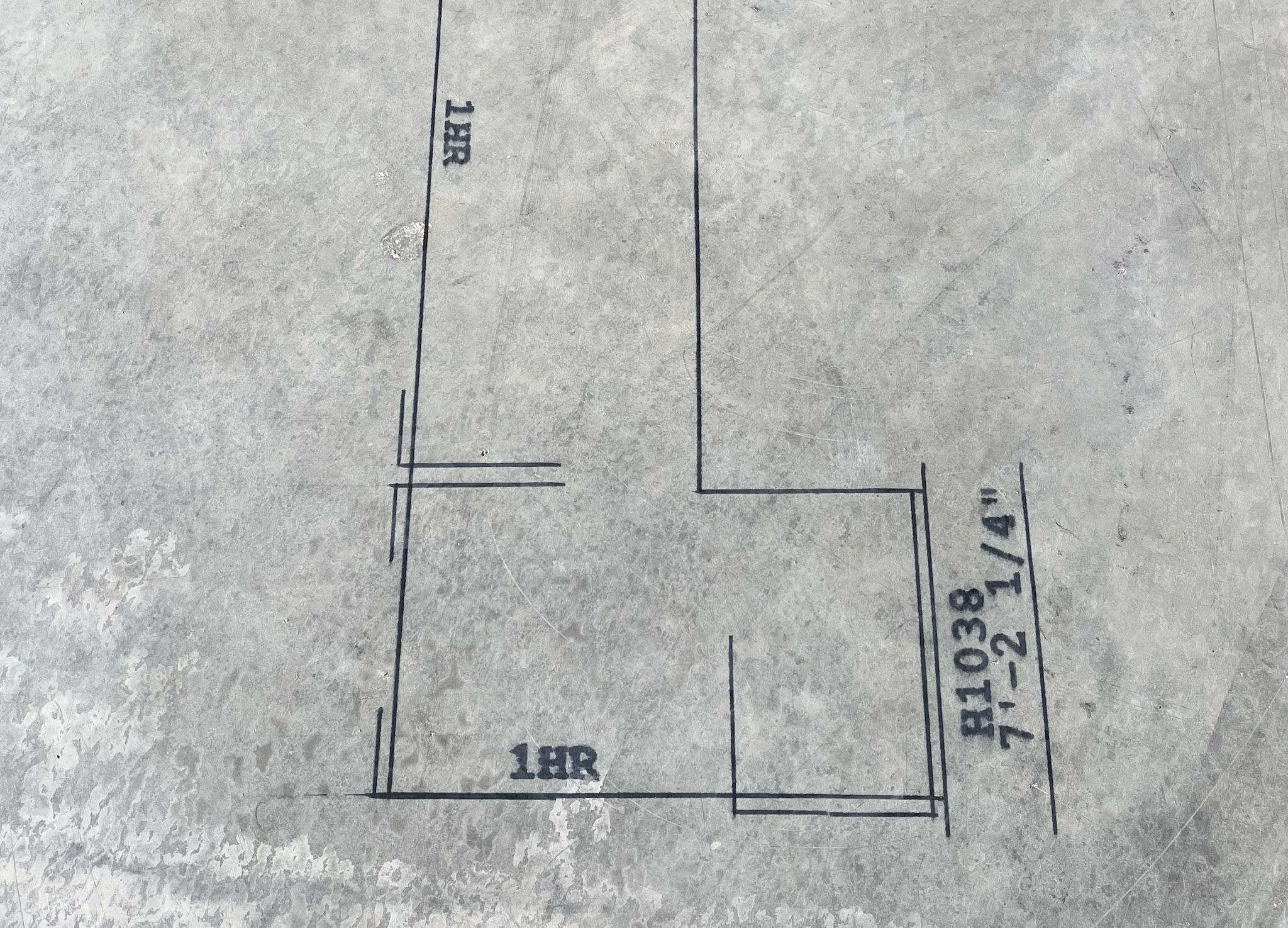
Thousands of Labor Hours Saved and Weeks off the Project Schedule
McCarthy and Performance Contracting Inc. relied on Dusty’s FieldPrinter to lay out 100,000 linear feet of linework, 36,000 points, and 22,000 text objects—all directly guiding field teams. The result? Less rework, greater efficiency, and tighter schedule control. Dusty flew through that layout, clocking over 150 MEP points or 500 linear feet of line per hour – each with descriptive text to aid installation.
According to Gonzalez, from the initial schedule, McCarthy “saved two weeks on a five-month layout schedule, while using only a four-person crew to lay out much more information than before. Previously each trade would have two separate four-person crews. Dusty let us be much more lean, accurate, and detailed, all at the same time.” Across the overall project, McCarthy estimated over 3,000 total labor hours were saved with automated layout compared to a manual layout process with chalk lines and total stations.
Win More Projects by Leading the Industry Forward
Beyond Kaiser Roseville, McCarthy’s success with Dusty has strengthened its relationship with Kaiser’s Northern California division.
“Kaiser wants us to maximize model-based workflows. With Dusty, we can show them that we’re executing the model in the field, which gives us a huge competitive advantage,” said Sullivan. “Kaiser even brought other contractors on-site to see what we were doing so they could implement it on future projects.”
“What Dusty is doing on this project is protecting the owner from spending money on rework. We're beating budgets based on what we've seen Dusty achieve,” Gonzalez said. “We’ve set a new baseline for efficiency. Kaiser is in expansion mode, and lessons from this project are shaping their future expectations.”
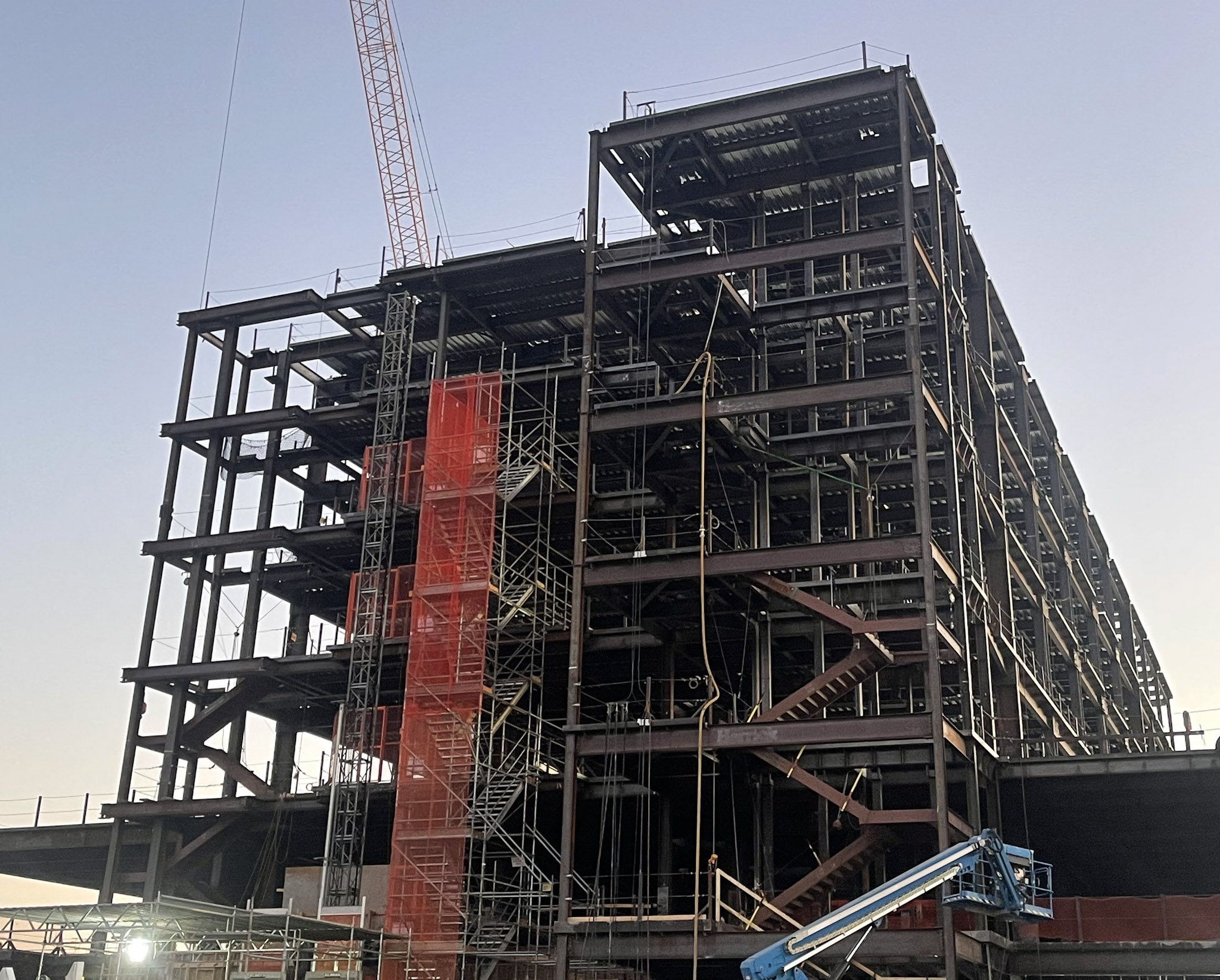
The Future of Construction is Automated Layout
Reflecting on industry transformation, Gonzalez shared, “When I started as a superintendent, I thought models were just for visualization—they never lined up in the field. Now, with Dusty, everything matches perfectly. Layout is the foundation of our success.”
Sullivan agreed, concluding, "with Dusty, we took the digital world and executed it one-to-one in the field. This level of automated layout will be the new industry standard".
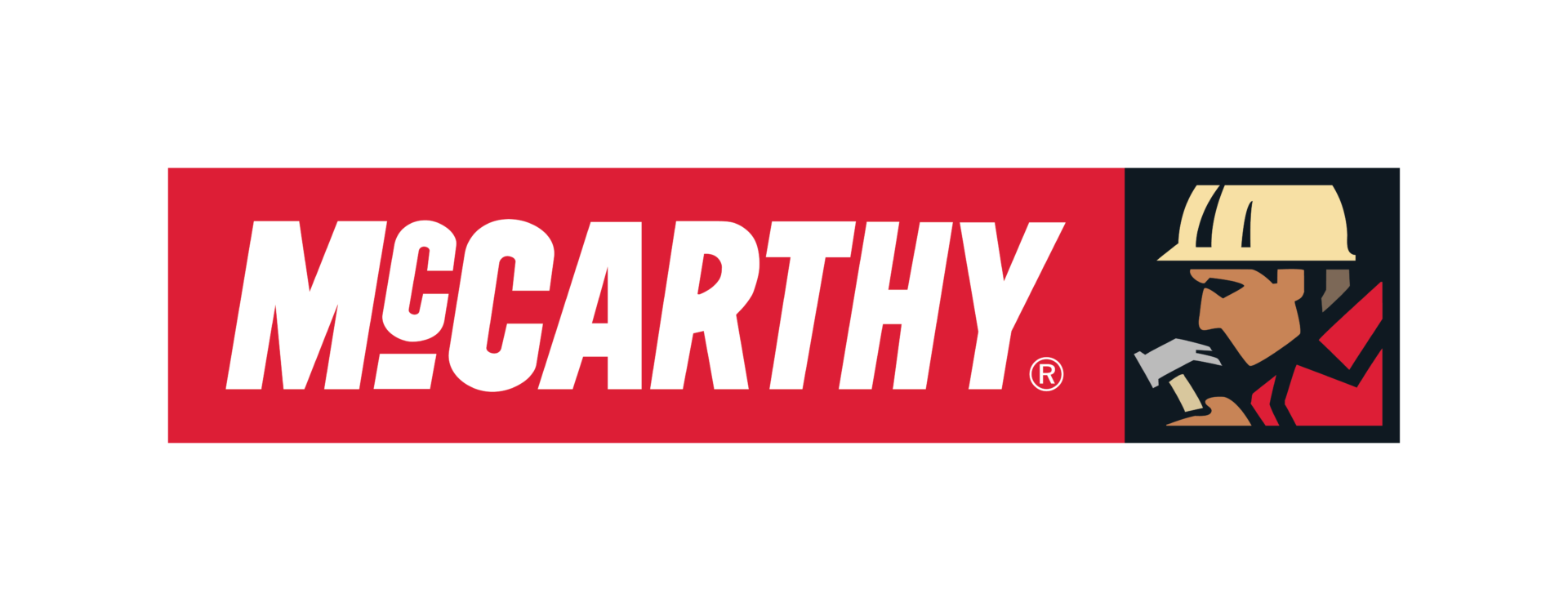
Interested in learning more about the
Dusty FieldPrinter?
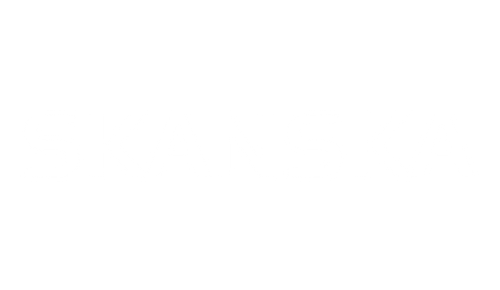
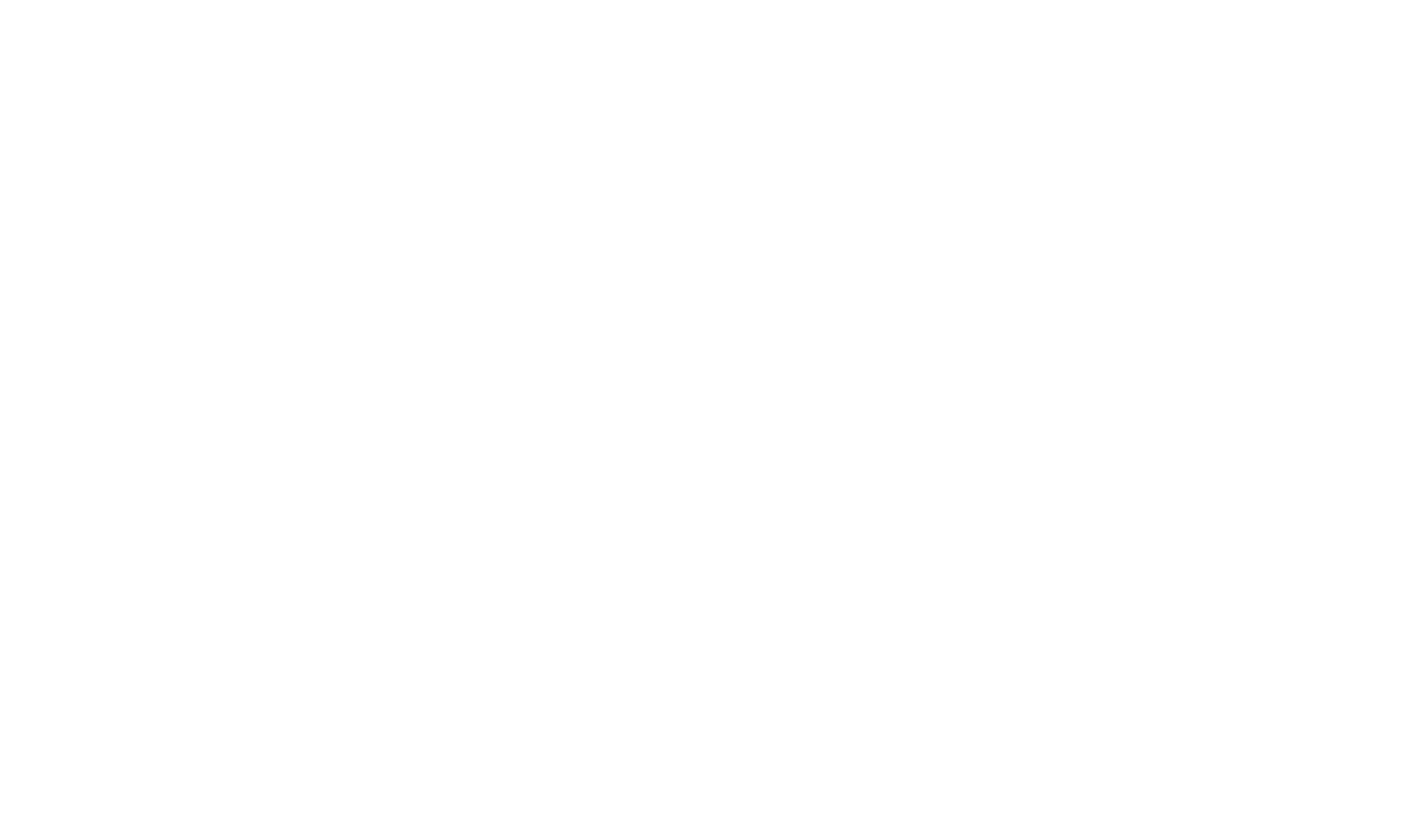
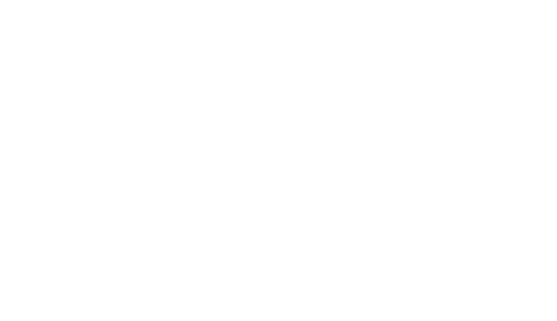
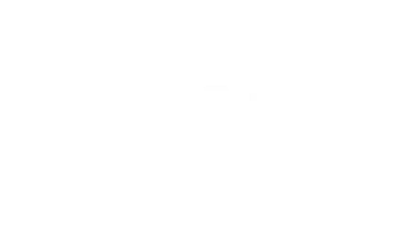
.png)
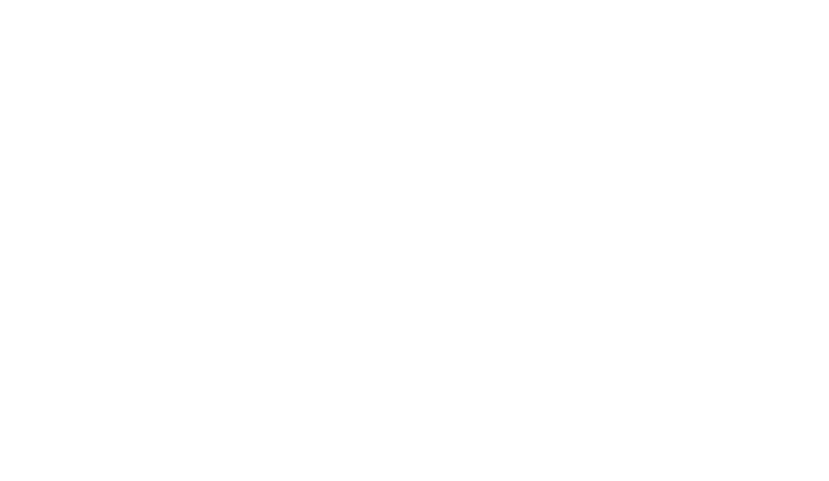