RG construction, a commercial wall and ceiling contractor who has brought operational excellence to projects across the midwest since 1977, had a challenge.
It had just been engaged by ENR top 20 general contractor Gilbane Construction on a major, $420 million 2-building expansion to the Cleveland Clinic’s Global Center for Pathogen and Human Health Research. The 296,000 SF project, which brings new exam rooms, research laboratories, dedicated classroom space, offices, a café, and a new entrance to the southeast section of the campus, provides a new home to the Clinic’s largest research initiative in its 100+ year history.
Luther Lampkin, director of technology and innovation at RG Construction, knew this was the moment for Dusty Robotics. “Once Dusty Robotics was fully integrated, the process became seamless. Its accuracy and efficiency transformed how we approached the Cleveland Clinic project, setting the foundation and new standards for large-scale construction,” Lampkin says.
Automated Fuels Prefabrication Strategy to Streamline Construction
One secret to RG’s success on the Cleveland Clinic project was prefabrication. The prefab strategy included 48 individual pods of six types, each measuring 10x26 feet. Each pod incorporated all necessary trades from drywall, millwork, and doors to mechanical, electrical, medical gas, and plumbing.
Lampkin knew the strategy hinged on perfect coordination, clarity and alignment between the trades, and accurate construction. So, he took Dusty into the prefab facility as well as onto the jobsite. The team used Dusty to lay out all coordinated trades for each module in the factory.
“The blueprint is on the ground,” Lampkin says. The construction efficiency took off, thanks to the clarity and completeness of information crews had available as they built. They were able to ensure that each pod was constructed to the exact specifications required for seamless integration into the building.
With prefabrication, RG minimized on-site disruptions and significantly reduced the time spent on installation, allowing for quicker assembly and fewer coordination challenges. They also increased safety by moving labor off the jobsite and into the more controlled factory environment.
Coordinating Layout Across Multiple Trades Ensures Quality
Thanks to advanced planning and careful coordination between the trades, and the accuracy with which Dusty laid out that information during prefabrication, the team drove a quality installation onsite. The team also used Dusty onsite for perfect alignment of sequential pods with the interior blade walls.
Faster Layout Leads to Overall Schedule Compression
“High quality doesn’t always mean efficiency, but Dusty combines the two. That makes using Dusty a no-brainer. When we brought in Dusty Robotics, it brought a level of transparency that most projects don’t have," Lampkin states. “This transparency is essential to ensure the entire team is on the same page and is working with up-to-date, accurate information, further enhancing safety on the jobsite.”
The traditional layout method was slow, inefficient, and prone to error. With Dusty in place, the team was able to lay out twice as many linear feet per day, using only one person instead of two. At the same time, RG put far more complete information on the floor.
“Dusty made the layout process four times faster,” said Lampkin. “We’re laying out twice as many linear feet, and we’re able to lay out all the other trades at the same time, which is a huge improvement.” So while the layout schedule got shorter, the amount of information surfaced to installation crews increased significantly.
That extra information and Dusty’s accuracy paid even bigger schedule dividends when crews started building. “That accuracy carried over into framing, helping everything come together quickly and correctly. We got so fast at it, we finished about four weeks ahead of schedule—all of the other trades had to catch up.”
Dusty’s Efficiency Helps Win New Contracts
This innovative approach also paved the way for future opportunities. Even before completing the Cleveland Clinic project, RG secured another major medical project—the Mayo Clinic–where they will also use Dusty Robotics.
RG now directly writes Dusty Robotics into the specifications for projects in partnership with their general contractors, because of the gains in quality and efficiency.
“Our strategy is to under-promise and over-deliver, and so far, we have been over-delivering with Dusty,” Lampkin says. “Dusty has broadened our horizons with business development.”
Dusty Inspires a Vision for the Future
As Lampkin sees it, Dusty integrates Building Information Modeling (BIM) into the real world and makes it possible for the teams building the real thing to finally benefit from the information in the model.
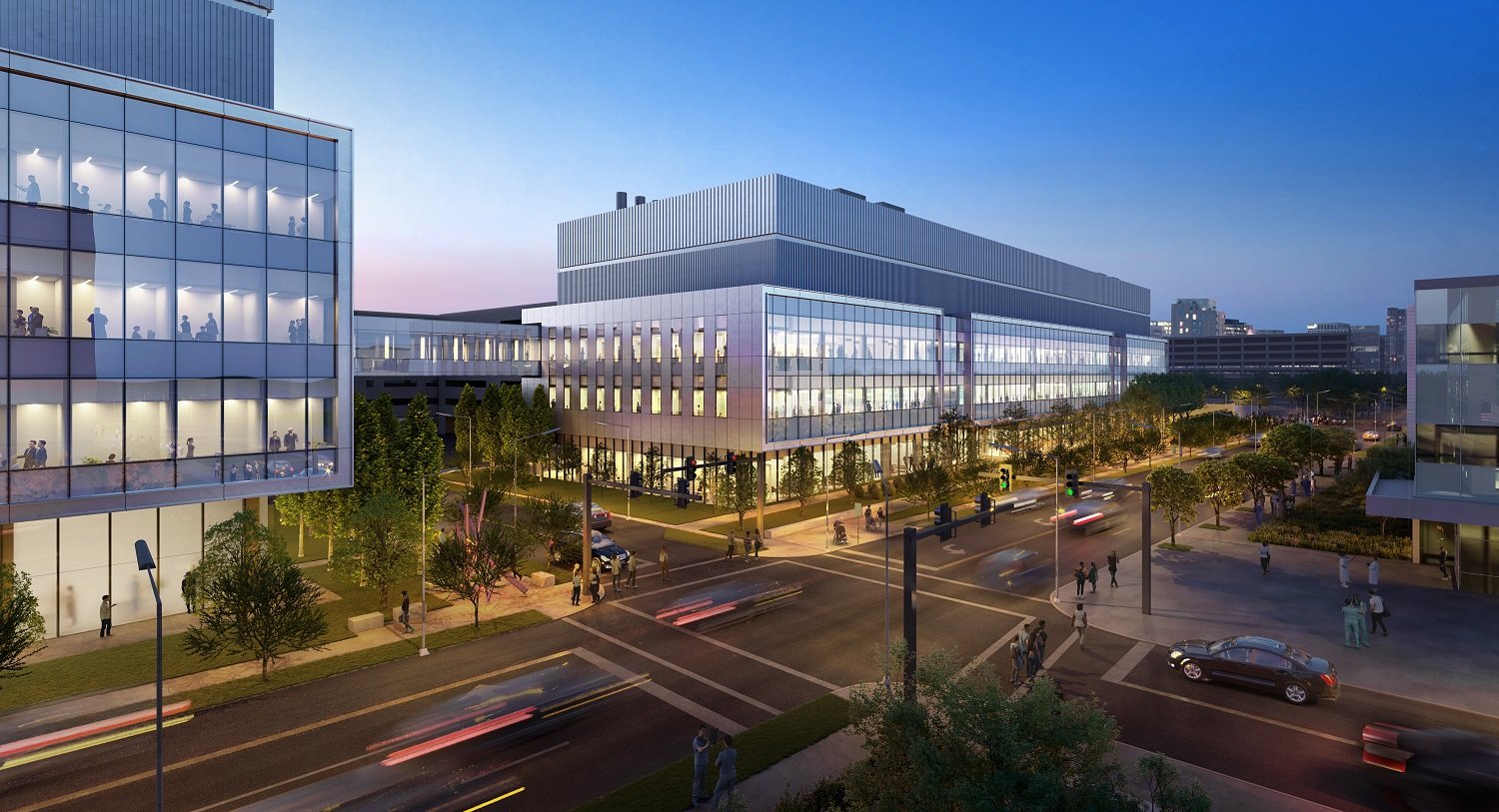
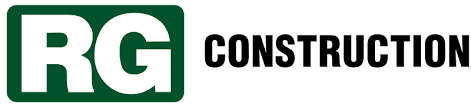
“Dusty brings all the trades together. From the warehouse to the jobsite, everything was coordinated—wall openings, access panels, door tags, finishes, you name it. With everything printed directly on the floor, trades didn’t have to chase down drawings, they could just look at the ground and know exactly what to do.”
Interested in learning more about the
Dusty FieldPrinter?
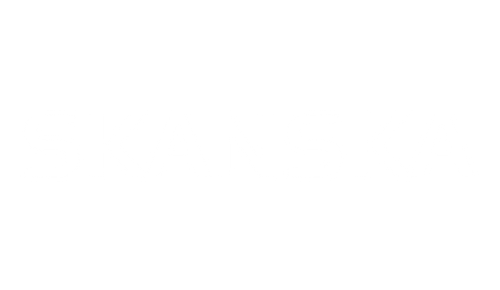
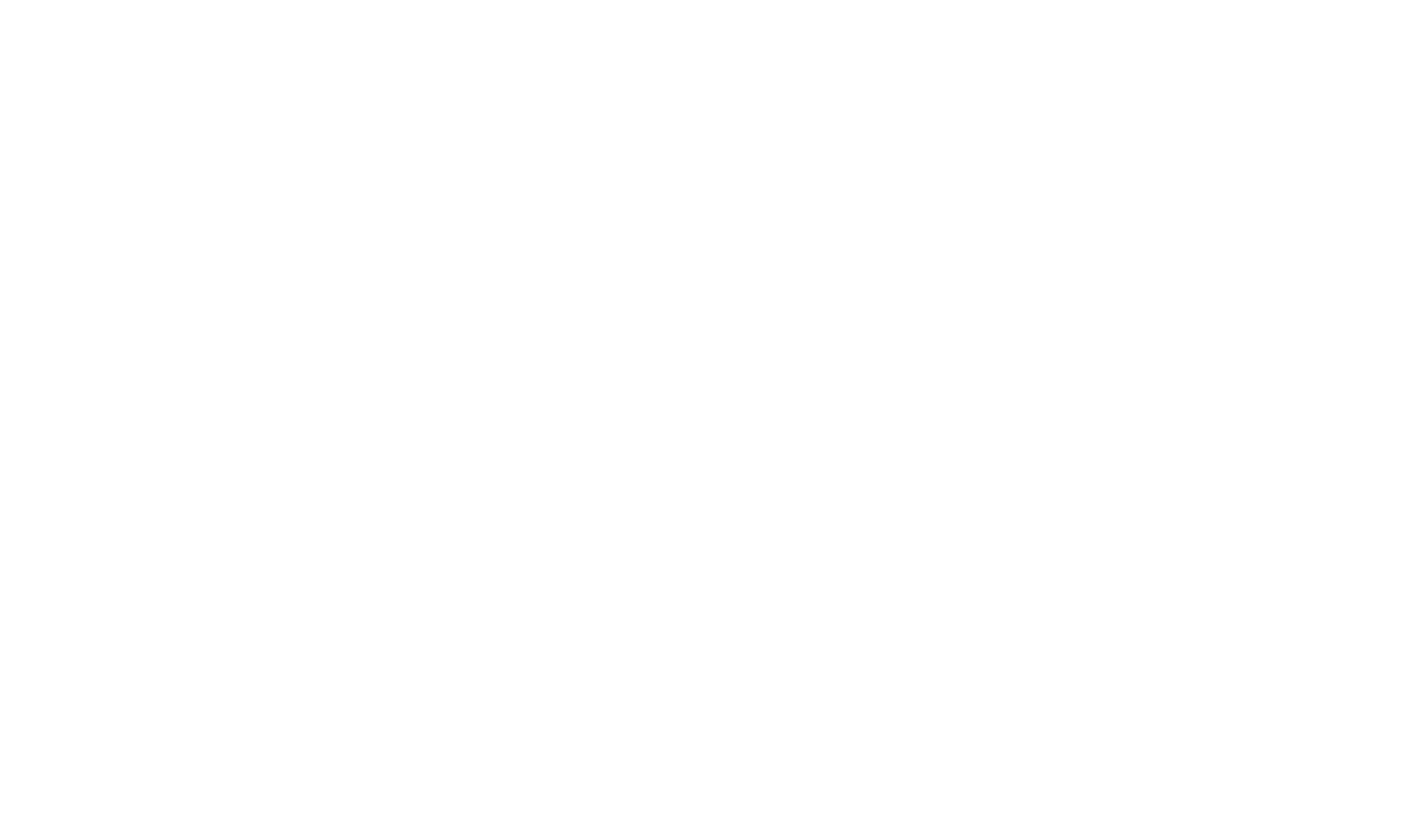
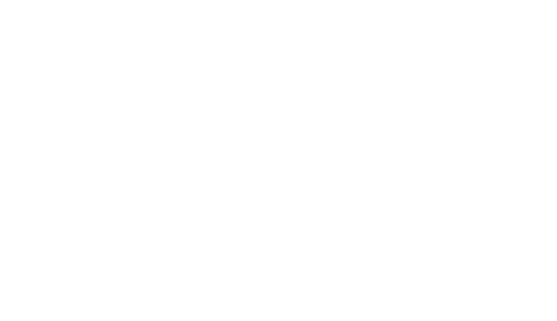
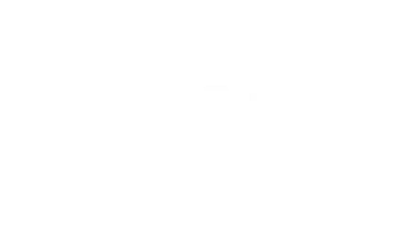
.png)
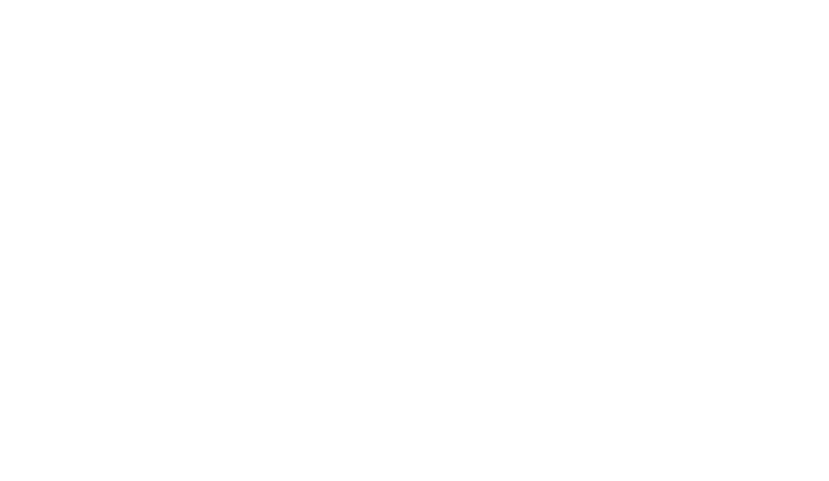